What do you understand by 3D Modeling? 3D modeling alludes to the process of making a mathematical representation or illustrations
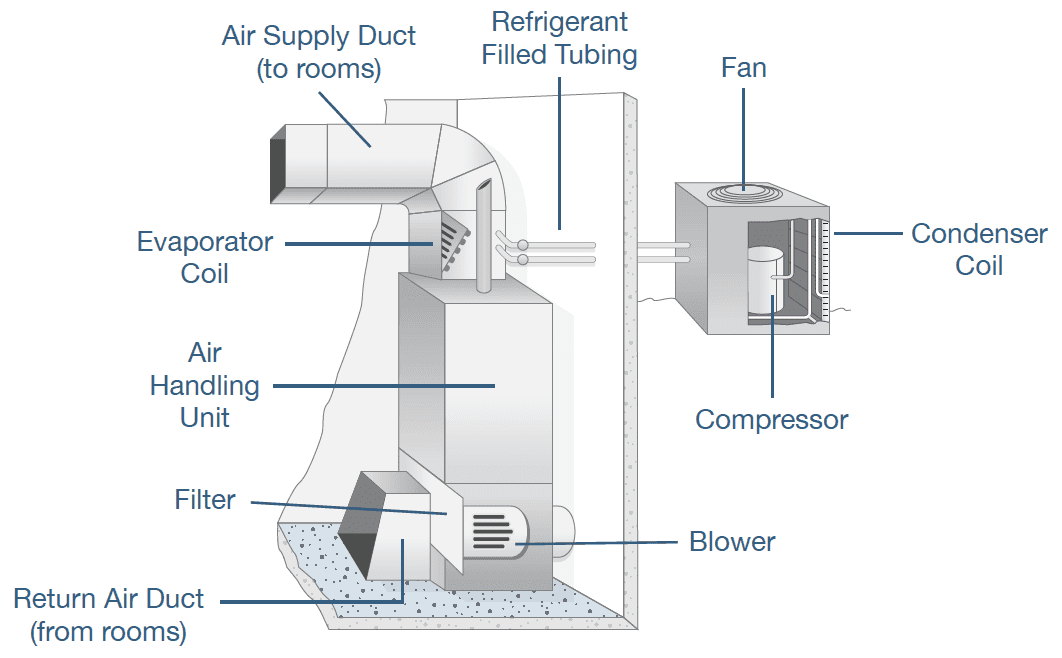
According to ISO 14644-1, HVAC system design is heavily dependent on the required clean room classroom classification, which leads to adopting specific Air Changes Number per Hour (ACH). ISO-14644-1 is considered the gold standard for cleanroom construction in the USA. While cleanroom standards do not always offer a clear roadmap on how to accomplish them, they help to measure and define the expected outcomes.
Without cleanroom ventilation, several important institutions and industries including medical devices, pharmaceutical, and biotech environments would need to shut down. This is because products like medical devices, microchips, and medicines should be manufactured in totally clean & germ-free indoor spaces. In addition, people’s lives and health would be at risk without clean room ventilation in these environments.
But, what exactly is Clean room ventilation? More importantly, how does it work and when do you need it?
Read on to find out!
Cleanroom ventilation refers to an HVAC system with a special type of air treatment, specifically designed to work in sealed areas that require dust-free indoor air, without microbiological contamination. It’s commonly used in the manufacturing process since the ambient air in these spaces should be free of air contaminants.
Here’s why clean room HVAC Design is important!
To start, the risk of contamination from airborne or dust particles is quite high in microelectronics and pharmaceutical production sites without clean room ventilation. As a result, the airborne contaminants can attach themselves to whatever is being produced. This can create a risk of contamination to patients in the case of pharmaceutical products or affect the usability of nanotechnology in microelectronics.
In addition, the air is usually a medium for airborne pollutants. These contaminants can come from within the facility, tools & materials we use, products being manufactured/ people in the space or outside. Clean room ventilation ensures that the space is free from all these contaminants. More importantly, it ensures that the facility meets all international standards, ISO classification, and Good Manufacturing Practice (GMP) standards, depending on the use of the products manufactured in the building.
Clean room HVAC Design can be crucial for various institutions like hospitals, electronic production, pharmaceutical industries, and biotechnology facilities. That said, clean rooms that should meet good manufacturing practices include; BioTech industries, pharmaceutical industries, and laboratories. While clean rooms for companies working in the production and research of laser & optics technology, aerospace industries and electronic hardware like hard drives, displays, and integrated circuits must meet ISO 14644. In addition, hospitals depend on the same techniques, although the standards are different.
The common thing about all these spaces is that air in cleanroom environments must be hygienic and free from dust and microbiological contamination. This is either due to the health of the people in that space or highly sensitive manufacturing processes.
A cleanroom environment requires an advanced ventilation system since there are several components you need to take into account. For instance, apart from ensuring that the air within the closed space is clean, it also needs to meet the right temperature, humidity, and velocity. Moreover, you have to ensure that the air is introduced into the room correctly and all surfaces inside the space are smooth & easy to clean.
According to ISO 14644-1 and Federal Industry Standard, there are four requirements for clean rooms. That is;
In essence, clean room ventilation design is a complex air treatment that must be done with great care by experts. Besides, it must meet the strictest hygienic requirements to ensure the health of other people as well as the material being used in that space.
The HVAC system is an important part of the cleanroom ventilation as it handles the indoor air quality including the humidity, temperature, airflow streams, room pressurization, CFM and air change per hour. Moreover, it helps the cleanroom to maintain a monitored level of contamination, which is specified by many particles per cubic meter with a specific particle size or viable bacteria.
With that in mind, cleanroom ventilation systems can either be installed with an auxiliary central air system or a dedicated modular system or connected to an existing HVAC system in the facility.
An existing HVAC system offers the most economical and effective way to cool a modular clean room. This is because filter/ fan units draw air from the surrounding room and pass it directly into the clean room without requiring special exhaust systems or ductwork. Moreover, the additional load on the existing HVAC is relatively easy to calculate by adding the heat produced by the specified number of filter/ fan units (FFUs) (about 1000 BTUs/ hr/ unit) and by people and equipment inside the clean room.
Modular systems can offer economical cooling in building facilities that don’t have adequate HVAC. The type and size of the modular system will depend on the desired temperature, cleanroom size as well as the heat produced in the cleanroom.
In these systems, heat removed from the space is vented into the room outside. However, in the case of significant heat-generating equipment or large cleanrooms, the vented room will put a greater load on the existing HVAC systems and A/C modules as well as increase the ambient temperature. For that reason, ventilation fans and exhaust ducts should be installed to vent heat outside the manufacturing facility to ensure the most efficient operation.
In the case of large modular cleanrooms, a split AC system is preferable to the AC modules as it moves the heat-generating compressor outside the manufacturing facility. Also, this will ensure that the facility gets a recirculation and ducting system that moves exhaust air to the AC system. This will deliver cooled feed air to the ceiling FFUs in an adequate volume to maintain the desired internal air velocity.
Vents and ducts direct air in a specified speed and direction. If any of these building features are blocked or closed, the room temperature becomes uncomfortable, while the air becomes stale. And in the case of cleanrooms and other controlled environments, safety and cleanliness will also be affected. In addition, if the amount of make-up air isn’t sufficient, CO2 can build up, thus endangering the health of the employees.
In cleanroom ventilation, ducting connects variable air return and AC systems to FFUs for balanced airflow and temperature control. This is the most efficient way to recirculate the air, especially in rooms without plenums. Generally, 12” is the typical diameter size for ductwork in cleanrooms.
However, ducting is recommended in small rooms, while plenums are more effective in larger cleanrooms. Either way, both ducting and plenums will need space behind walls and above the ceiling. Moreover, ducting should be kept in straight lines to minimize the build-up of static pressure and improve the overall efficiency of the HVAC system.
On the other hand, vents provide a way to eliminate hazardous or noxious vapors or fumes and relieve pressure. Also, they can be manipulated to allow less or more air through them, while baffles help to control the volume and direct air.
The cleanliness and aerodynamic performance of a cleanroom environment largely depend on the room pressure, containment integrity, and the efficient removal/ introduction of air through the fan filter units and HVAC system. In addition, air leaks due to cracks, windows, doorways, and gaps are expected in a positive pressure environment and must be put into consideration when determining the requirements of air supply.
However, hazardous and pharmaceutical environments encounter greater adversity when managing and designing component integrity and construction processes of cleanroom environments. Not to forget that the installation, delivery, and manufacturing process may present some level of cracks and apertures that are invisible to the naked eye.
On the downside, air leakage can be particularly challenging for negative pressure containment rooms, especially if the application involves aseptic workflows or sterile preparation. Typically, negative pressure rooms draw air from a dedicated air supply system and exhaust air to the outdoor environment. The extra pressure tends to increase leakage coming from window seals, doors, and wall panel gaps, as well as within air returns and ducting.
As a result, poor containment integrity can cause various problems such as inadequate ventilation rates, safety concerns, moisture/ heat transfer, inability to clean/ filter the incoming air, and unpredictable airflow patterns. So, as the rate of leakage increases, the rate of air supply must also increase to maintain the pressure differential and minimum air change rates.
It’s important to consider the design, operation, and mounting of doors in cleanroom environments to maintain pressure differentials and cleanliness throughout parallel areas. Moreover, door operation is a key factor when assessing potential sources of contamination under working conditions.
Research (link: http://www.ncbi.nlm.nih.gov/ ) shows that opening cleanroom doors more slowly helps to prevent air flow equalization. In addition, studies show that the angle to which the cleanroom door is opened, the velocity of the door opening as well as air temperature and density will affect the ability of the doors in cleanroom environments to control contamination.
Air pressure balancing in cleanroom environments is the process of establishing a specific room pressure target after compensating for room leakage and exhaust air. A hazardous or sterile room may need a pressure difference of up to 0.6” water (15 pa), while non-critical rooms may only need a pressure difference of about 0.28 – 0.32” water (7 to 8 pa). Typically, cleanrooms that need a pressure difference of more than 0.” water will need an area of intermediate pressure or airlock between them.
Cleanroom facilities usually include multiple partitions or rooms, each with a respective air quality requirement and specific purpose. When these environments share a wall or are connected, the pressure levels and airflow in each room have to be designed to avoid transmission of contaminants into adjacent rooms. The easiest way to accomplish this is by implementing cascading pressure differentials.
Conclusion
Creating Cleanroom ventilation is one of the most important, but complex challenges for air treatment. For that, it’s important to involve an expert who knows clean room ventilation well when creating a clean room.
At InnoDez Design & Engineering, we can manage every detail of your clean room HVAC Design, thanks to our understanding of the interactions and technical challenges in cleanroom ventilation design. In addition, our HVAC experts will propose the ideal solution that works for your industry to ensure that the implementation of the cleanroom system design is correct and flawless!
including the components needed for an advanced clean room HVAC Design!
Also, thermal loads have to be addressed in the early project stages, putting all external and internal heat sources into consideration. For that reason, thermal load calculation is needed to understand load fluctuations and for HVAC equipment selection to choose the most feasible HVAC system for any building.
About Author
Fate Ol