The Marvelous World of MEP Engineering Ah, MEP Engineering! If buildings were superheroes, MEP systems would be their capes—often overlooked
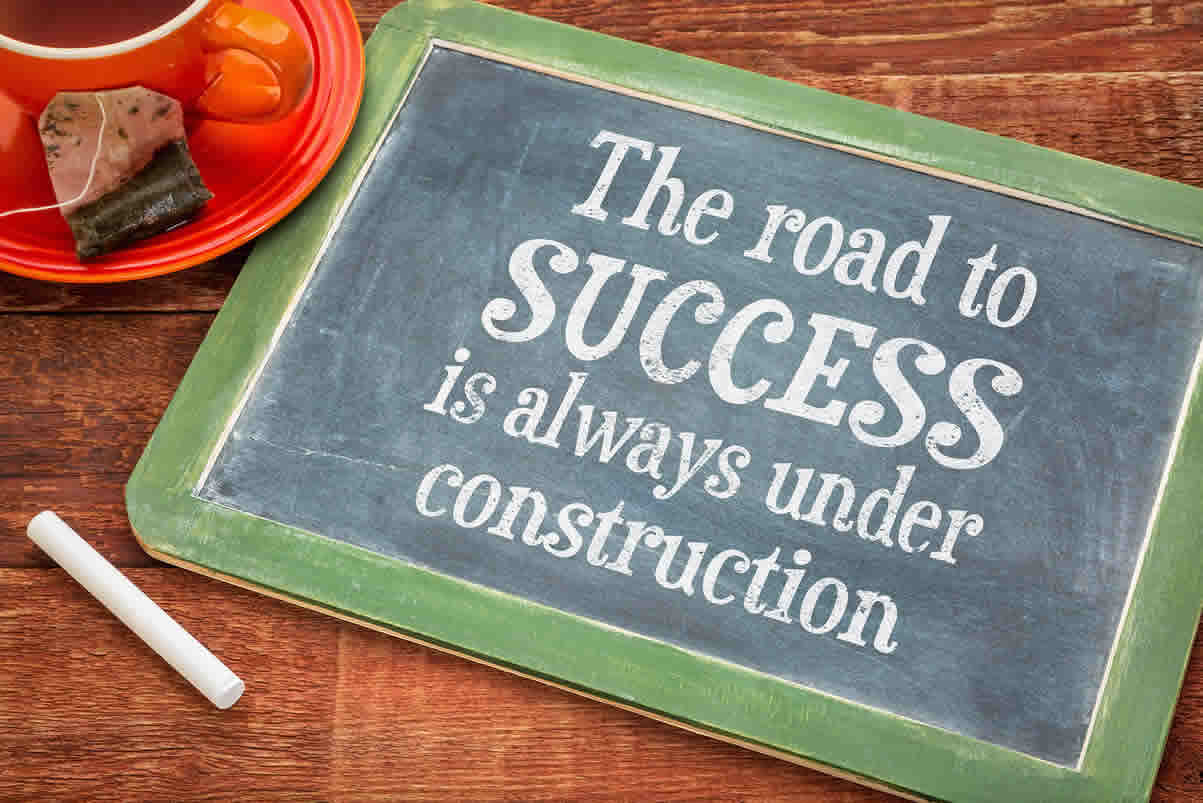
Coronavirus has changed communities worldwide. With over 15 million cases reported as of July 28, and the number is still increasing! Companies and governments worldwide are responding to this pandemic fast. But there is much more that they need to do.
During these hard times, the world needs the construction industry now more than ever! From donating lifesaving equipment to building hospitals with the shortest time possible. The construction sector has been vital in responding to the COVID-19 crisis. And we will still need it in the recovery, especially since it represents about 13% of the global GDP.
But the sector was also affected. With construction sites in several nations closing. While the open sites facing disruption in operation restrictions and supply chains. As a result, the financial indexes of construction-related companies have decreased.
Now, let us go back to the 2008 financial crisis. During that crisis, firms that were able to come out ahead had to take certain actions. The actions included the rapid reallocation of resources, cost reduction, and early diversification.
Likewise, during the current crisis, companies must plan their moves now. Especially if they want to emerge ahead later! For the construction industry, returning to normal business seems like an unlikely scenario. Hence, leaders should prepare for what this sector will look like post-pandemic! In the meantime, 7 actions might help them to adapt and forecast the new normal!
Coronavirus has had a short-term economic downtown impact on the construction industry demand. And the crisis is even expected to affect the long-term demand and supply. This will result in permanent shifts in investment trends.
In comparison to the economy, the construction industry is much more unstable. When economic activities decrease, the new industrial and commercial facilities’ demand also decreases. While income loss also affects the demand for refurbishments and housing construction.
But, uncommon public-relief programs can support fast recovery and promote public-investment projects.
Moreover, this pandemic represents an impact to supply. Since domestic and migrant construction workers might be unable to access the sites. And they must observe the new on-site policies. Thus, reducing productivity for the forecasted future. Also, the supply chains of some construction materials have faced interruption. Hence suspending distribution and production.
Engineering, construction, and building’s (ECB) performance was lower than that of other sectors, even before Coronavirus. Low profitability, productivity, and digitalization have been persistent in this industry for long. Not to forget a high level of manual labor on-site and fragmented ecosystem.
The recent years have indeed signaled imminent disruption. This includes labor scarcity, rising cost pressure, sustainability requirements, and new digital tools. Combining these factors is pushing the construction industry towards innovation.
A forthcoming evaluation includes an extensive analysis of over 400 ECB executives. The evaluation shows that this impact will shift the distribution of the value pools. So, incumbents must adapt their business models and strategies to existing in the ECB sector.
According to preliminary indications, most characteristics of Coronavirus pandemic are causing some disruption. Besides the immediate patterns, we expect lasting ones to increase. As new working and living ways become normal:
Short Term Trends
Increased digitalization:
Most organizations in the construction industry are moving to remote working ways. For instance, engineers and designers are relying on digital collaboration programs like BIM. Contractors are turning to online platforms. They are using them to check their workers’ health, maintain cash flow, and order materials.
Offset supply chains towards flexibility (versus efficiency):
Most contractors are looking for alternative suppliers. They are also building inventory and securing long-lead and critical materials.
Augmented Consolidation:
Constriction industry stakeholders are focusing on establishing economies of scale. They are also promoting investment in talent, technology, IT, and R & D.
Stakeholders are already adapting vertical integration. This will promote increased efficiency and control/ standardization of design and implementation. This might even promote greater resilience in a post-pandemic world.
The construction industry was experiencing a skilled labor shortage even before the pandemic. With the social-distance policies and movement restrictions, the shortage will become more critical. But there are tools like 4D simulation, real-time progress monitoring, and workflow management. These digital tools are important in increasing productivity. And their use will become even more power after the pandemic.
During this pandemic, close movement management and workforce interaction are necessary. Thus, making building in a controlled surrounding is making more sense. Such a principle further strengthens off-site construction techniques. Not forgetting the existing speed and quality benefits they pose. We expect to observe contractors shift to off-site fabrication. And manufacturers extend their scope of prefabricated subassemblies.
Governments might encourage carbon emissions reduction measures to stimulate the economy. Such incentives may include direct public investments and policy changes. We expect a parallel change in demand for more sustainable buildings. As well as communities that encourage healthier lifestyles.
ECB firms are already adapting steps that will help them move past the COVID-19 crisis. Most executives are reshaping their operating procedures and strategies. They are also launching visionary initiatives. This will help them emerge stronger and stimulate positive change during this pandemic. Leaders must also reshape their strategies to increase their chances of future success! To prepare for the new normal, leaders should consider taking the following actions:
Construction players do not have the time to develop the perfect strategy. So, organizations must adopt the well-proven use of remote programs. For contractors, this might include adjusting to remote collaboration during the production phases. While distributors should rethink the whole fulfillment model. This is through limited physical interactions, particularly through e-commerce models.
Balancing health and performance is always critical. And it is even much more important during these uncertain times. Thus, industry stakeholders must invest in culture. This prevents problems of remote working and workforce apprehension on productivity/ job security.
Construction prices are likely to come under pressure. In that case, firms must use their total size so that they do not get squeezed. In the coming days and months, resource allocation will affect the construction industry. This might cause trade-offs between assets and projects. And it will depend on accurate data across the firm’s portfolio. Thus, firms must develop a central monitoring operation. The operation should recognize and respond to the needs of resource-allocation.
Most stakeholders have already analyzed their supply chains’ susceptibility because of the pandemic. They are looking for options like building inventory, direct labor & alternative distribution channels. This can result in vertical integration and greater consolidation of their value chain. Thus, minimizing risk and boosting future productivity.
For the post-pandemic revival, stakeholders must develop strategies that focus on their business. Responding to this pandemic can provide opportunities to establish lasting strategies. But aspects will vary across value chains. They have options to deploy resources, capital, and capabilities in a viable manner.
Client preferences are experiencing a significant change. For instance, they are moving towards remote working and online retail. It is not clear what other changes might emerge. But we can speculate most of them will become normalized in client preferences, for life. For that, it is important to stay closer to current and future clients, now more than ever!
Subcontractors and suppliers should identify subsystems and elements that can be pre-assembled off-site. For the longer term, stakeholders should find more significant elements to build off-site. This will help manufacturers to collaborate and develop new products. Hence, ease activities on the construction sites. Moreover, off-site construction will promote sustainability goals. For instance, it will reduce materials waste, air dust, and noise pollution.
About Author
InnoDez