Before engineers start the planning and designing stage of any project, they have to decide what tools and materials are
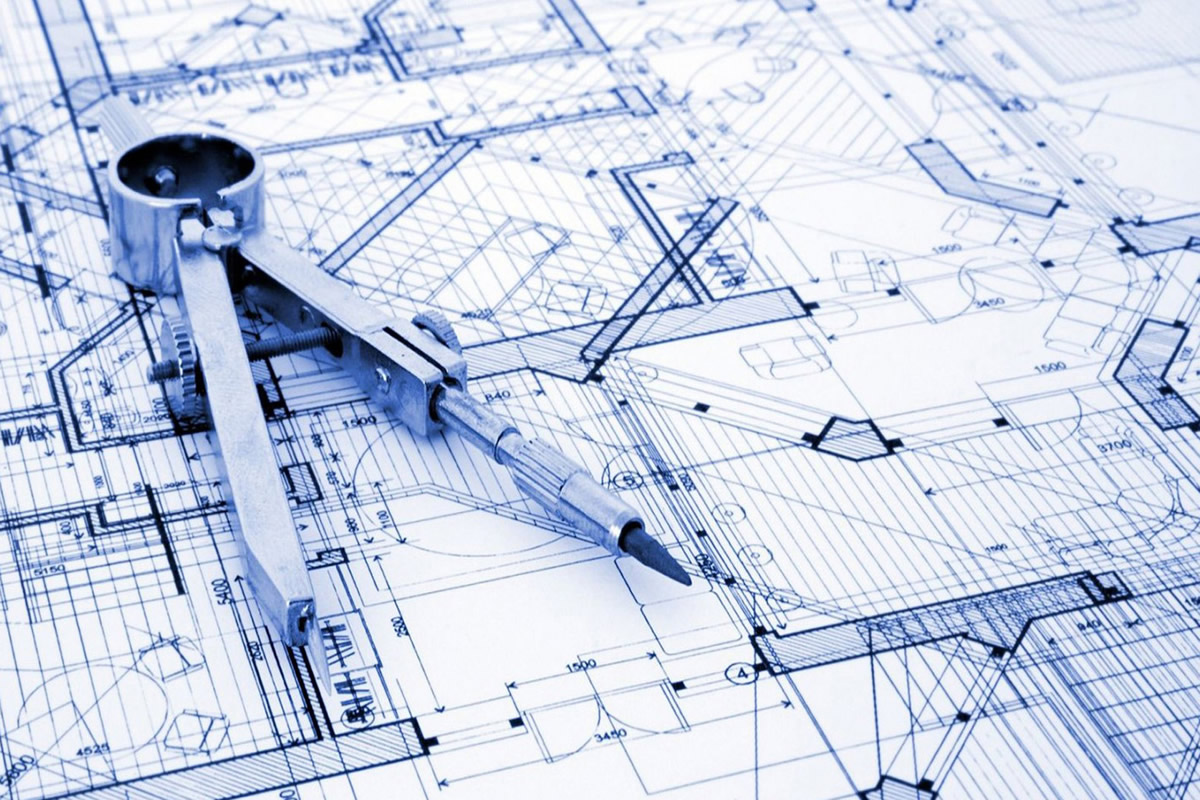
Building systems designs can quickly become crowded with information with more than one system drawn out in them. This makes it difficult to read and work with. Especially in office buildings, where electrical wiring, lighting fixtures, communication networks, and air conditioning ducts all get installed above the dropped ceiling. A more active approach is to draw out separate drawings for each building system. This creates design requirements that are easier to understand while limiting interpretation errors at the same time.
The drawings required to represent the building and the various systems that it contains will grow in relationship with the project scale. Construction plans can be more manageable when separated into sets such as:
Electrical Mechanical Architectural Structural
All building designs get presented to the local authority for inspection. This ensures that they are code compliant and that zoning requirements get met before a building permit gets issued. In New York City, only a Registered Architect (RA) or Professional Engineer (PE) can present plans for approval. The authority in NYC is the New York City Department of Buildings.
Are you in need of professional MEP design services for your new project?
Architectural drawings show the appearance of buildings: sections, floor plans, interior, and exterior elevations. They also outline any information needed to give the builder a clear picture of how the finished design needs to look. By working with an expert architect, you can be positive that the drawings are clearly understood. You can also ensure that the designs comply with any applicable building codes.
Structural drawings illustrate the structure's physical support design. They look almost identical to architectural drawings. They illustrate the same floor plans, sections, elevations, and other details. The structural drawings define the construction components needed to sustain the dead load of the structure. (and the live load of its occupants and contents.) Structures must hold enough strength to resist weather conditions like wind and snow, and severe weather events like tropical storms and earthquakes.
All structural designs are strictly governed by local and federal building codes. There must be an accurate account of forms and dimensions connecting architectural and structural drawings.
These drawings illustrate the power systems that carry electricity to building equipment and appliances. Electrical engineers draw the electrical drawings out. Electrical layouts show the position of visible components such as power outlets, switches, and lighting fixtures. They illustrate the conduit and the wiring that deliver voltage to these components. These components are generally concealed in walls or out of sight, above ceilings.
Additionally, electrical drawings present a full account of the distribution boards that circuits obtain power from. This includes the capabilities of the main feeders and circuit breakers.
Combustion-based heating systems are also equipped with electrical components. Components like pumps, fans, and their power supplies all get defined in electrical drawings. When structures use resistance heaters or heat pumps, the demand for electricity needed to heat them rises. Circuits then get matched to accommodate.
Standards and codes govern all electrical projects. Only compliant designs get approved by the New York City Department of Buildings.
The NFPA 70 National Electrical Code determines the requirements for all electrical system installations in the United States. In New York City, there is a separate Electrical Code that covers the entire NEC with any special amendments and requirements.
Electrical components require the mark of either or Intertek Electrical Testing Laboratories (ETL) or Underwriters Laboratories. (UL) Their marks show that the component has passed a rigorous test for safety.
Electricians at work in the project must be familiar with the codes, the needed materials, and the equipment going into the project. This is to ensure that they can install the electrical system as outlined in the design. If the structure gets damaged by fire and the electrical system cannot comply with code, insurance companies will not cover the project.
Energy efficiency marks such as NEMA, Premium Efficiency, and ENERGY STAR are not obligatory. However, you can achieve a significant reduction in operating expenses if the equipment that you purchase has them. Additionally, a vast majority of energy efficiency incentives apply for labeled equipment only. For instance, Con Edison lighting incentives only apply to fixtures and lamps bearing ENERGY STAR or DesignLights Consortium (DLC) marks on them.
As indicated by their name, mechanical drawings present the design and technical specifications for all mechanical operations in a project. This includes air conditioning, heating, ventilation, plumbing, fire protection, and sheet metal. Because there are many systems and equipment varieties involved, many of the drawings get supplied by subcontractors upon permission of the architect.
Plumbing drawings present the layout for wastewater and potable water piping. The drawings also include domestic hot water (DHW) systems, which generally utilize natural gas as their heat source. The drawings also include any vents and storm drain diagrams.
The Uniform Plumbing Code serves as the national standard during the design process. There are additional city-specific ordinances such as the NYC Plumbing Code to comply with.
The NYC Fuel Gas Code also applies to hot water systems based on combustion.
Plumbers study the drawings in detail before continuing with their part of the installation. Many plumbing elements are set in the floors and walls of the structure. This makes them more challenging to adjust than HVAC and electrical installations.
Additionally, plumbing systems carry both clean water and wastewater. This means that defects in the system carry the potential to create health hazards in a very short period. There are substantial penalties for New York City plumbing code violations. This is one of the reasons why plumbing contractors endure a rigorous licensing process before they ever work on an actual project.
HVAC drawings define the location and installation aspects of all cooling, heating, and ventilation devices. They additionally provide the layout for sheet metal ducts utilized in air distribution systems.
Sheet metal design must be very specific to guarantee the correct installation. This is because ducts have numerous curves and connections. For this reason, they must get verified at multiple locations.
HVAC systems may utilize hydronic or steam piping depending on their method of installation.
Pipes and air ducts require proper sizing to deliver the needed air conditioning and space heating output for the building areas that they serve.
The hydronic piping design and sheet metal are dependent on heating and cooling loads. For this reason, an exact load estimate is extremely important. In the end, a correct design that contains inadequate data can lead to an unsatisfactory design.
Installing external equipment such as boilers, chillers or furnaces isn't the biggest challenge in HVAC systems. The biggest challenge of the installation is ductwork and hydronic piping. This is because they both travel long distances with changes of direction and accessories. Mechanical drawings need to clearly state the details of the layout and the details of the installation of these systems.
The design of the HVAC is strongly related to the efficiency of the building envelope. If the structure is properly insulated and airtight, both heating and cooling loads drop. It is much simpler to add a high-performance building envelope to a new project than upgrading existing property where walls were previously built.
Gutters Conveyors Machinery guards and hoods Flashing needed to components from water damage Any canopies and decks
As-Built Drawings and Shop Drawings include layouts of work done away from the job site. The subcontractors normally prepare them. Shop designs need to include very high detail, with a sufficiently large enough scale to display all of their relevant features. These drawings are then authorized by the design architect before the fabrication of any of the corresponding works.
As-built drawings show exactly how to assemble all building structures after the completion of the project. The installation of components in slightly different positions generally will not affect the performance of the component. This means that for ease of installation or convenience, contractors can make minor modifications as needed. Suggestions for such modifications in as-built drawings should be presented to the architect.
Overhead valves Cleanouts Junction boxes, conduit, and conductors Underground piping
As-built drawings give you a reference to work with for maintenance, repairs, and alterations. The drawings are essential for all building systems, but especially for plumbing, HVAC, and electrical installs.
Construction drawings are necessary during the entire lifespan of a structure. In addition to specifications, they allow highly effective communication of project criteria to both contractors and their teams.
As soon as the project is finished, design documents are used to examine the structure and any installations carried out on the design. When structures are finished and operating, construction plans are extremely valuable during maintenance exercises or system improvements. Just be sure that the drawings are up to date following every change.
About Author
InnoDez