Sustainability in construction is no longer a trend; it's a necessity. As the world grapples with environmental challenges, the construction
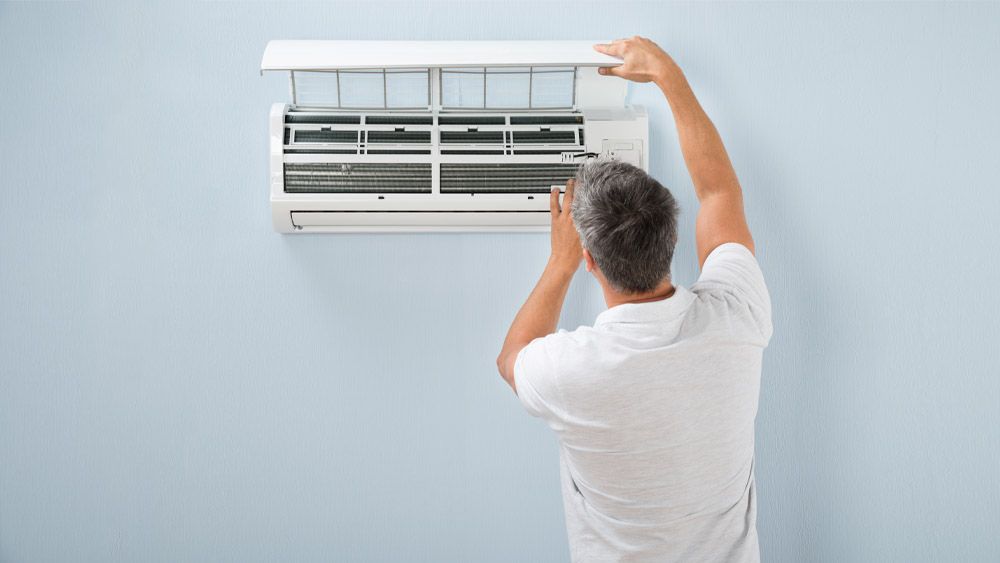
PERC (Perchloroethylene) is an effective and the most commonly used solvent in dry cleaning shops in the United States. Unfortunately, PERC is a volatile organic solvent that may pose serious hazards to workers if exposure isn’t properly controlled. For instance, at high levels, PERC vapors can cause workers to feel sleepy, dizzy, or have headaches and nausea.
Therefore, it’s important for employers to protect workers in dry cleaning shops from PERC exposure. In addition, a PERC dry cleaning shop should take the necessary steps to contain dangerous chemicals from PERC vapors and prevent them from escaping into neighboring businesses and homes. More importantly, dry cleaners must follow local, state, and federal regulations, and maintain low levels of PERC vapors in their shops.
In this article, we’ll look at the best practices and regulations dry cleaning businesses should follow to protect workers and building occupants from dry cleaning chemicals and equipment.
As the name implies, a vapor barrier room restricts the movement and diffusion of PERC vapors that escape from dry cleaning equipment. A ventilation fan then collects these vapors and extracts them through a stack above the building.
These rooms are required by Regulation 11, Rule 16 for co-residential PERC dry cleaning facilities to reduce exposure to PERC vapors and the associated health risk. In addition, VBRs may be required for new non-residential dry cleaning facilities that emit high levels of PERC to adjacent occupational or residential buildings.
A vapor barrier room for dry cleaning facilities should be constructed from materials that can resist the diffusion of solvent vapors. This includes materials like; sheet metal (recommended), heavy plastic sheeting sandwiched between gypsum (drywall) sheers, or metal foil-faced insulation sheets. In addition, gaps and seams for multiple layers of materials should be sealed with aluminized tape, instead of standard duct tape at each layer.
Make sure you contact your county/ city building department and pull a permit for the construction of the VBR and electrical work. Moreover, some materials for VBRs may need to be covered with drywall sheets to meet building code and fire code requirements. Not to forget that some building codes have minimum dimensions for access aisles and doors for vapor barrier rooms. For instance, you should allow at least 3 ft clear between the front & back of a dry cleaning machine and new walls and about 32” clear for doors.
Talking of doors, vapor barriers should be equipped with self-closing devices to ensure they’re normally closed. These doors may either have a ‘swinging’ or sliding door design and should have plastic strips to cover the doorway if the door is opened for an extended period of operation. Windows can be installed in walls or doors to allow light or for make-up air and should either feature tempered glass or plexiglass for safety reasons.
Fresh make-up air can be supplied to the dry cleaning shop through gaps around the entry door or adjustable louvers/ sliding windows. It’s recommended that makeup be introduced at the same height as the loading doors and at the front of the dry cleaning machine. Moreover, the ventilation fan/ duct should be installed at the rear of the vapor barrier room or near the ceiling directly above the back of the dry cleaning machine.
An exhaust fan may either be installed inside the vapor barrier room or outside the building on the roof or on a wall. This fan should run continuously in a co-residential facility and have a high-pressure design with a minimum capacity of 1000 CFM. More notably, the stack should extend at least 5 ft above any adjacent roof and at least 30 ft from any window/ air intake.
A Local Ventilation System (LVS) or Partial Vapor Room may be required for existing non-residential buildings that install an additional PERC dry cleaning equipment or increase their PERC usage limit. However, a Vapor Barrier Room is more effective for capturing emissions and is highly recommended for shopping malls and multi-story buildings.
Similar to Vapor barrier rooms, PVR materials should be resistant to the diffusion of solvent vapors. This may include heavy plastic sandwiched between drywall sheets or metal foil-faced insulation sheeting. In addition, gaps and seals should be sealed with aluminized tape and windows should be made from Plexiglass to allow light and for safety reasons.
Some dry cleaning facilities may require Local Ventilation Systems (shrouds and fume hoods) to capture harmful emissions. In that case, the sides of the fume hoods should have plastic strip curtains to provide better capture velocity and reduce cross-flow draft. The plastic strip curtains should extend at least 3 ft at the back or in front of the dry cleaning machine, while the exhaust fan should be mounted behind/ above the machine close to the ceiling. In addition, the exhaust point should be at least 5 ft above the adjacent building or dry cleaning facility and 30 ft from any air intake/ window.
Dry cleaning facilities that use local ventilation systems as control should have an inward air velocity of 100 fpm through the unloading and loading door. This velocity provides a draft of clean air passing over the items being removed from the dry cleaning machine, helping to minimize PERC vapors escaping into the dry cleaning shop. In addition, exhaust from the dry cleaning equipment should be ducted at least 5 ft above the room to prevent the vapors from entering adjacent buildings or the dry cleaning facility.
Conclusion
Vapor diffusion is the major cause of background ambient air Perchloroethylene concentrations throughout a dry cleaning shop. For that reason, it’s important to create a dry cleaning ventilation design that reduces vapor diffusion and the vapor level reaching the breathing zone of the workers.
At InnoDez Design & Engineering, we’re committed to helping dry cleaning facilities in California control PERC vapors to minimize their release into the environment and prevent subsequent worker exposure.
About Author
InnoDez