A little (400 to 1000 square feet) or minuscule (under 400 square feet) protected substantial structure (ICF) home is energy-proficient,
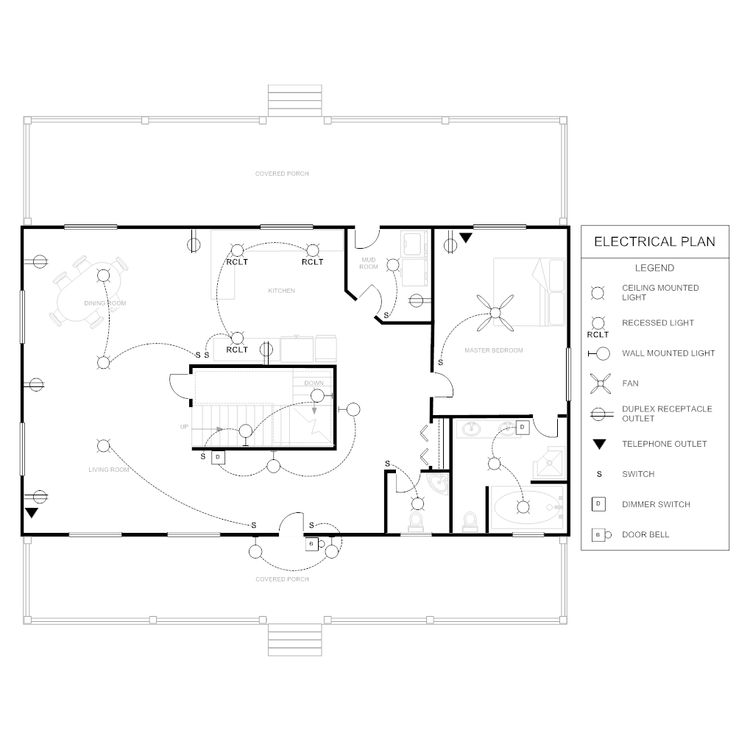
Over the years, commercial garage facilities have been experiencing serious safety hazards due to their potential for explosion and fire. For instance, service pits in the facilities have been trapping workers under burning vehicles, leading to electrocutions and terrible injuries because of the concentration of water and many flammable liquids.
While gasoline is usually the main culprit in these accidents, hydrogen can also be dangerous, both as a vapor and as a fuel. Similarly, propane and compressed natural gas as well as volatile hydrocarbons also present a safety hazard. Not to forget other flammable liquids that are found in commercial garages like kerosene, grease, and diesel fuel.
Due to these underlying dangers, commercial garage facilities are classified as Class 1 Division 1 zones. Moreover, most facilities that are under construction are preferring above-slab fits, while many older structures have discontinued their pits in an attempt to mitigate these risks.
However, this step alone may not be enough, considering there is still extensive use of electricity for arc welding, lighting, battery charging equipment, and power tools in the facility. For that reason, the electrical design for commercial garages must be flawless. In this article, we’ll tell you what is involved in creating electrical design and wiring commercial garages!
The design of a commercial garage facility should address all aspects of the proposed construction. The 1st step of the design process should be to size out the service, including the general lighting load for different occupancies.
In general, every square foot of a commercial garage requires 0.5 VA. While this may not seem like much, this figure doesn’t include the receptacle load as is the case with dwelling units. Instead, it’s added along with other loads. Besides, the 0.5 A per sq ft is only intended for lighting. Therefore, the electrical design for a commercial garage has to consider all receptacles and other equipment, including motors when calculating the total load.
If any of the motors has a rating of more than 5HP, or if you’re planning to perform heavy arc welding work in the facility, you should consider installing a 3-phase electrical service. In addition, you have to meet with the electric utility in the early design stages to agree on the rate structure, type of service, and where the service drop will hit the garage building.
For a large garage building, more than 100 ft long, you may want one or more sub-panels and feeders to reduce voltage drop. Every structural metal, metal ductwork, airline, and water pipe should be strongly attached back at the main bonding jumper’s service neutral. This will help to separate the equipment-grounding conductor and the grounded neutral. In addition, branch circuits higher than 18” above the slab should be placed in MC and EMT or flexible conduit. That way, continuous ventilation will not be required, and a wide range of mechanical work including major engine overhauls and fuel tank changes will be allowed.
Any classified area with a commercial garage facility is designed according to Art. 511.3 (B). Moreover, such areas must conform with Art 514 (Motor Fuel Dispensing Facilities) in the event that flammable fuels are dispensed into fuel tanks outside or inside the garage building.
Spray rooms for car painting in commercial garage facilities must comply with Spray Application, Dipping & Coating Processes (Article 516). For instance, you can locate all lighting behind indestructible transparent or translucent panels instead of creating an electrical design in accordance with Class 1 specifications. All wiring should be partitioned from the interior of the automotive spray painting room as well as any motors and equipment that run ventilation fans. In addition, spray fumes should be separated from any air intake or fire source and vented to a dedicated area outside high above grade.
If these spaces are effectively partitioned from the service areas in the commercial garage building, they should be excluded from the classified zone area. However, the door sills in their entries should be more than 18” above the garage floors, something that should be addressed in the early design stages so that it reflects on the foundation plan.
Batteries being charged and battery-charging equipment must be done in partitioned rooms with a fairly large floor area and high ceilings to allow hydrogen to dissipate. In addition, these rooms should be vented away from the service area.
Similarly, welding rooms should be partitioned off the service area with the non-combustible wall material. Moreover, they should be equipped with receptacles sized to match the welding equipment that will be used and hardwired back to the service panel with no additional disconnect.
Apart from explosion and fire hazards, electric shock is another serious danger lurking in a commercial garage building. Luckily, you can offset this hazard by code compliance.
According to the code, all single-phase, 125V, 15A & 20A in garages that use electrical hand tools, portable lighting equipment, or electrical diagnostic equipment, must have GFCI protection. You can easily achieve this by installing receptacle-type devices or circuit breakers. In addition, explosion and fire hazards caused by electrical wiring coming into contact with liquid fuels and flammable gas in commercial garages can be mitigated by installing wiring outside the classified areas.
Low voltage wiring is increasingly becoming a part of the scope of work for electrical design for commercial garages. For instance, properly grounded telephone and internet cables must enter the facility at an appropriate place depending on external parameters and be distributed to their points of use.
Lastly, lighting a commercial garage building can create challenges for electrical designers, low-bay lighting fixtures are recommended for ceiling heights that don’t exceed 16 ft. While high-bay fixtures are ideal for ceiling heights that are taller than 20 ft. In addition, ordinary cool white fluorescent fixtures can be used for high-use areas and workbenches.
Whichever the case, lighting for commercial garages must be carefully zoned to ensure that the whole building isn’t lit at once. Instead, 3- and 4-way switching should be included in the electrical design for walk-through lighting, and a few T8 fixtures should be unswitched to ensure the building is never in complete darkness. Moreover, battery-powered emergency lighting fixtures should be connected to unswitched lighting circuits.
Final Word
Careful planning and design of electrical systems for commercial garages can prevent property loss and human injury in the future, creating a profitable & efficient working environment. To install a safe electrical system in your facility, make sure you follow the requirements we’ve mentioned above when retrofitting, building, or designing a commercial garage.
Alternatively, you can just call InnoDez Design and Engineering, especially if your commercial garage is in California. Our experienced and certified electrical designers have the experience needed to undertake your electrical panel upgrade project to ensure the lighting system in your facility is safe and efficient!
About Author
InnoDez