A modular building is a prefabricated building that consists of repeated sections called modules. Modularity involves constructing sections away from
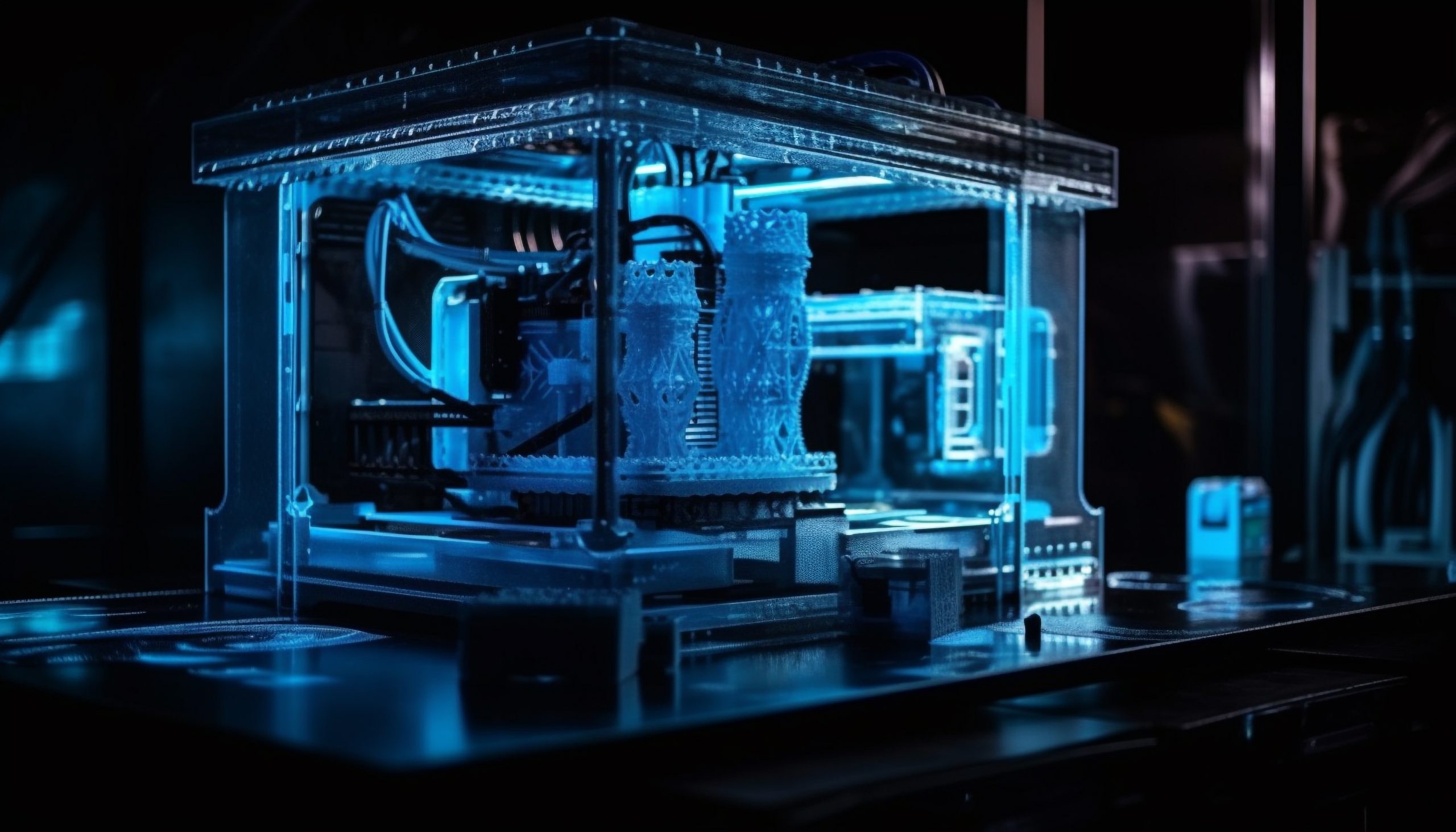
In the ever-evolving field of construction and engineering, technology continues to play a pivotal role in advancing design and fabrication processes. One of the most significant technological innovations in recent years has been the development of 3D printing, also known as additive manufacturing. This technology is increasingly being adopted in various sectors, including the mechanical, electrical, and plumbing (MEP) industry, where it is transforming the way MEP components are designed and fabricated.
MEP systems are the backbone of any building, responsible for heating, ventilation, air conditioning (HVAC), electrical power distribution, plumbing, and fire safety systems. These systems require precise and complex components, often custom-made to meet specific building requirements. Traditionally, the fabrication of MEP components has been labor-intensive, time-consuming, and prone to errors. However, with the advent of printing, these challenges are being addressed, offering new opportunities for efficiency, customization, and sustainability. This article explores how printing is transforming MEP component fabrication and how InnoDez, a leading MEP design company, is leveraging this technology to enhance building performance and design.
3D printing, originally developed for prototyping in the manufacturing industry, has rapidly expanded its applications in construction and engineering. The ability to create highly detailed, custom components using various materials has made it an ideal tool for the complex needs of MEP systems. In recent years, 3D printing technology has matured to the point where it can produce not only small components but also large-scale building elements.
For MEP engineering, printing offers a way to optimize the design and production of components such as ductwork, pipe fittings, electrical enclosures, and even custom HVAC parts. The technology allows for greater flexibility in design, enabling engineers to create components that are perfectly tailored to the unique specifications of a project. Moreover, 3D printing reduces the need for traditional manufacturing processes, which can be slow and costly.
InnoDez, a leading provider of MEP design services, has been at the forefront of integrating 3D printing technology into their projects. By embracing this innovative approach, InnoDez has been able to deliver cutting-edge solutions that enhance the efficiency and sustainability of building systems. Their expertise in MEP design, combined with the capabilities of printing, has allowed them to optimize the fabrication process, reduce waste, and improve overall project outcomes.
One of the most significant advantages of printing in MEP component fabrication is the ability to create highly customized parts with extreme precision. In traditional manufacturing, creating custom components often requires specialized molds or tooling, which can be expensive and time-consuming. With 3D printing, engineers can design components with intricate geometries and produce them directly from digital models.
This level of customization is particularly valuable in MEP systems, where components must often be adapted to fit specific building layouts or meet unique performance requirements. For example, HVAC systems often require ductwork with non-standard shapes or pipe fittings with complex angles. 3D printing allows for the seamless production of these components, ensuring that they fit perfectly into the overall system.
Traditional fabrication methods for MEP components can be slow, particularly when custom parts are required. The process of designing, creating molds, and manufacturing parts can take weeks or even months, depending on the complexity of the project. 3D printing, on the other hand, can significantly reduce production times.
With 3D printing, digital models of components can be created quickly, and the printing process itself is much faster than traditional manufacturing. This allows MEP engineers to prototype and test components rapidly, making adjustments as needed without the delays associated with retooling or reordering parts. The result is a more efficient design and fabrication process, which can help reduce project timelines and costs.
3D printing can also lead to significant cost savings in MEP component fabrication. Traditional manufacturing processes often involve high upfront costs, particularly for custom components that require specialized molds or tooling. Additionally, the materials used in traditional manufacturing are often wasted due to the subtractive nature of the process, where excess material is removed to create the final product.
In contrast, printing is an additive process, meaning that material is only added where it is needed. This reduces waste and lowers material costs. Furthermore, the ability to print custom components on-demand eliminates the need for expensive molds and tooling, making printing a cost-effective solution for producing both standard and custom MEP components.
Sustainability is a key consideration in modern construction, and 3D printing can play a significant role in reducing material waste. Traditional fabrication methods often result in a significant amount of waste material, particularly when components are cut or shaped from larger blocks of material. This waste not only increases costs but also has a negative impact on the environment.
Because 3D printing is an additive process, it uses only the material required to create the component, significantly reducing waste. Additionally, many printing materials are recyclable, further contributing to the sustainability of the process. By reducing material waste, printing helps MEP engineers create more environmentally friendly building systems, aligning with the growing emphasis on sustainable construction practices.
The digital nature of printing allows for enhanced collaboration between MEP engineers, architects, and contractors. Digital models of components can be easily shared and modified, facilitating communication and coordination across different teams. This collaborative approach helps ensure that MEP systems are seamlessly integrated into the overall building design.
InnoDez, for example, leverages printing technology to enhance collaboration with their clients and partners. By providing digital models of MEP components, they can work closely with architects and contractors to ensure that the systems they design are optimized for the specific needs of the project. This collaborative approach not only improves the efficiency of the design process but also fosters innovation, as teams can experiment with new ideas and solutions more easily.
Traditional manufacturing methods often impose limitations on the complexity of the components that can be produced. This is particularly true for MEP systems, where components such as ductwork and pipe fittings may require complex shapes and geometries to fit within tight spaces or meet specific performance requirements.
3D printing, however, allows for the creation of components with complex geometries that would be difficult or impossible to produce using traditional methods. This flexibility enables MEP engineers to design components that are optimized for both performance and space utilization. Additionally, printing can produce lightweight components by incorporating internal lattice structures, which reduce material usage without compromising strength or durability. These lightweight components are easier to transport and install, further improving the efficiency of the construction process.
The use of 3D printing in MEP component fabrication is already having a significant impact on various aspects of building design and construction. Some of the key applications of 3D printing in MEP engineering include:
While 3D printing offers numerous benefits for MEP component fabrication, there are still challenges to overcome. One of the main challenges is the limited range of materials that can be used in 3D printing. While the technology is advancing rapidly, some MEP components require materials that are not yet compatible with 3D printing.
Another challenge is the scalability of 3D printing for large-scale construction projects. While printing is well-suited for producing small to medium-sized components, larger components may still require traditional manufacturing methods. However, as 3D printing technology continues to evolve, it is likely that these challenges will be addressed, further expanding the potential of 3D printing in MEP engineering.
3D printing is revolutionizing the way MEP components are designed and fabricated, offering new opportunities for customization, efficiency, and sustainability. InnoDez, as a leader in MEP design, is harnessing the power of 3D printing to deliver innovative solutions that enhance building performance and reduce costs. As the technology continues to advance, the role of 3D printing in MEP engineering will only grow, shaping the future of construction and building systems for years to come.
About Author
Xhuljo Jakup