Benefits of Implementing Renewable Energy Solutions In today's era of environmental awareness and sustainability, incorporating renewable energy solutions in MEP
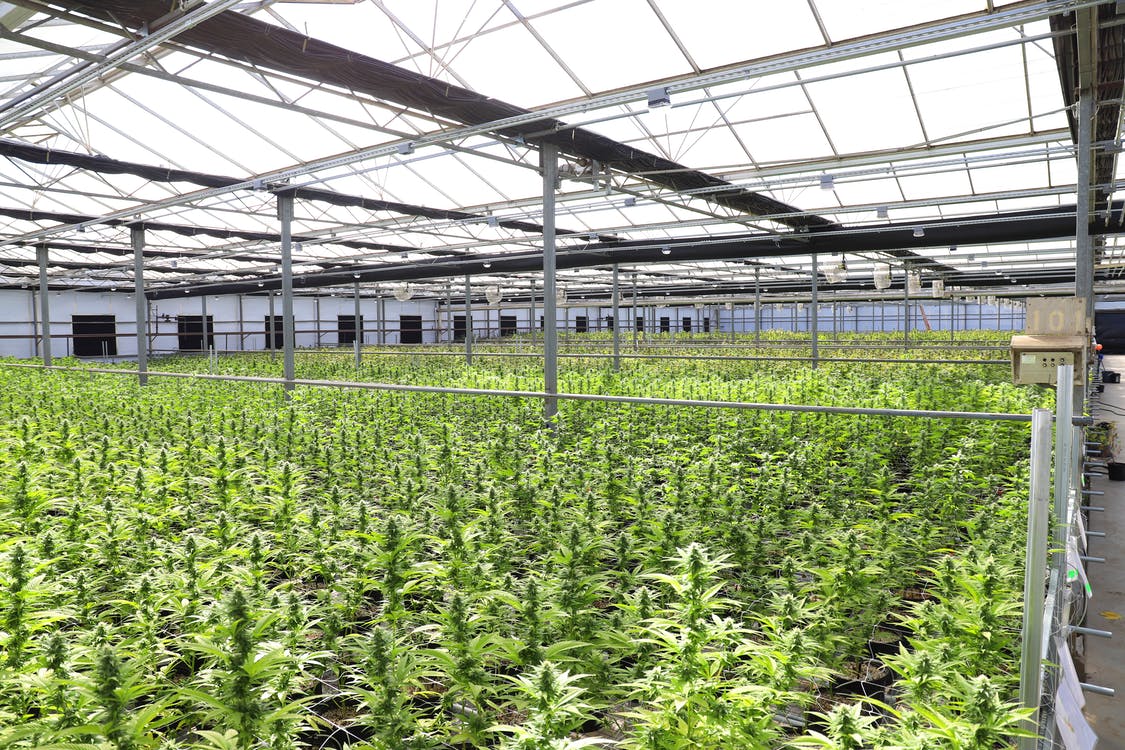
HVAC ventilation design strategies can be the difference between the failure or success of a cannabis cultivation facility. Currently, HVAC designers are dependent on manufacturers with flourishing applications since the ASHRAE is yet to establish guidelines for this emerging industry.
As a result, the strategies for HVAC design for cannabis cultivation facilities vary greatly to include a wide range of environmental conditions. This includes conditions that are essential for the growth of cannabis plants like temperature, humidity, and lighting duration. Unfortunately, master growers are hesitant to share information and ventilation strategies that have led to the success of their environmental conditions.
Luckily, in this post, we’ll show you some HVAC design strategies that may determine the success or failure of your cannabis grow facility!
Let’s get started!
Metal duct Vs Fabric duct
The use of metal ducts vs fabric ducts in flowering/ grow rooms is becoming increasingly popular in many grow facilities. Specifically, growers are shifting towards fabric ducts to prevent biological contaminants including mold & mildew may grow on the exterior and interior surfaces of metal ducts.
Also, this prevents condensation which occurs in metal ducts since grow rooms are usually conditioned at 50 – 70% RH and 75 – 80 deg F. On the same note, metal ducts used in these conditions require single-wall or double-wall wrapped in insulation, thus increasing the material costs.
On the contrary, fabric ducts utilize many fundamental strategies to prevent mold growth and condensation. As an example, the duct may be designed as permeable, allowing air to penetrate the fabric weave. Consequently, air flows over the whole duct surface, helping to prevent condensation. In addition, fabric ducts do not need special coatings or insulation to protect them against rust or corrosion.
Structural concerns and condensation consequences
Another negative impact of using metal ducts in ventilation design for cannabis cultivation facilities is that zinc is used in their galvanization process. Condensation dissolves this zinc out of the ducts and drips into the soil below. The cannabis plants then absorb zinc from the soil, creating a harmful effect when inhaled or burned. Besides, industry regulatory tests examine for traces of heavy metal elements. Thereafter, plants that test positive for heavy metal trace elements are destroyed.
Renovating former industrial structures is quite common in the cannabis industry. However, it requires growers to demolish the interiors and install new HVAC systems. When designing retrofits, you have to ensure that the existing roof structure can support the proposed duct. Most existing buildings are not typically designed to support tons of extra metal ducts for new HVAC systems. Luckily, fabric ducts are lighter than metal ducts and don’t need structural or seismic considerations.
Understanding airflow strategies for sensitive cannabis grow rooms
There are many stages involved in cannabis cultivation and each has its own environmental and room conditions. Although fabric ducts can be used in all environments, it’s very important for flowering or growing rooms. Grow rooms are perceived as a severe environment due to the relatively high RH & heat and the critical nature of cannabis plants.
Master growers determine the ideal environmental conditions to incorporate into their recipe to ensure optimal productive growth. In most cases, they prefer airflow that gets rid of microclimates on top of the plants, without delivering too much cold air that may shock them.
Similar to their metal counterparts, fabric ducts provide various dispersion methods. Typically, the vents are positioned along the length of the duct as linear arrays. This provides a more even air dispersion that is better than the typical registers of 5 – 10 ft increments used in metal ducts.
In addition, growers need to consider the placement of the ducts in relation to the lighting systems. Generally, ducts are installed above lighting systems to prevent shading. However, these systems emit heat that may create a thermal barrier. For that reason, the air discharge velocity should have the ability to penetrate that thermal barrier to get to the canopy. While doing so, care should be taken to avoid blowing at the lights directly since it may affect the lights’ output spectrum. In essence, the air discharge should reach the canopy at a velocity of 150-CFM.
Air distribution & Ventilation design for cannabis cultivation facilities
Duct runs installed over the plants instead of a room perimeter system are extremely popular and effective. On the other hand, air handling units can be floor-standing, ceiling-mounted, or installed outside the walls. This design is suitable for growing rooms since the system doesn’t need return air ductwork. Instead, the return air strategies may simply comprise grills on every unit throughout the grow room.
The return air strategy will pull air from each side of the room, preventing cold & hot spots, humidity buildup, or air stratification. Therefore, it’s a smart design with metal or fabric, but the latter’s ability to ensure uniform air distribution increases the efficiency of that option.
Besides, you can suspend fabric ducts from the structure in various ways. The best suspension technique will depend on the specifics of the growth space. For instance, single cable systems are the most affordable to buy and the easiest to install for straight ducts. While flush-mounted T-rail suspension systems are ideal for ducts installed close to the ceiling. More notably, these systems allow convenient removal for cleaning & maintenance.
Conclusion
Overall, fabric ducts are superior to metal ducts in terms of air distribution, cleanability, and lightweight. In addition, they ensure significant labor-saving and energy-saving, making them ideal for use in ventilation design for cannabis cultivation facilities. For instance, they reduce installation labor by 40- 70% and lead to enhanced energy efficiency compared to metal systems. Both factors can affect the project and operational costs.
About Author
InnoDez