Introduction In today's rapidly changing world, the importance of sustainability cannot be understated. As the global commitment to combat climate
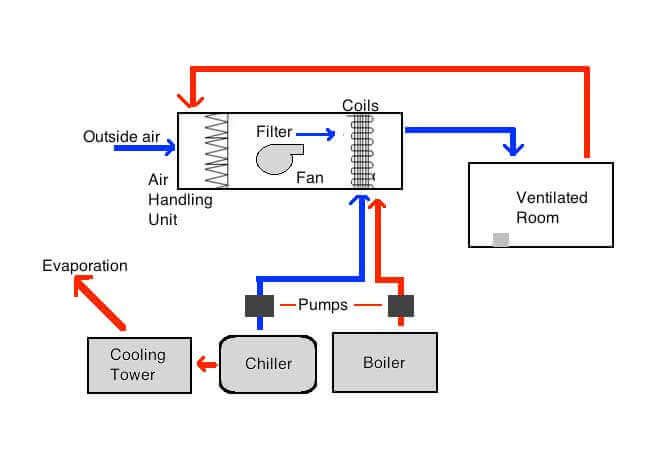
Most products processed and manufactured in clean room system design environments such as electrical components and pharmaceutical products tend to be moisture-sensitive. For that reason, the clean room specifications must include precise Relative Humidity (RH) control. This will play a crucial role in influencing the productivity and efficiency of sensitive items manufactured in these spaces while protecting the integrity of your product and process.
If the relative humidity is too high, metal equipment/ products can corrode, bacterial growth can flourish and water absorption & condensation can occur. On the other hand, if the humidity is too low, static discharge and buildup can become a problem. Not to mention that poorly controlled humidity makes the working space uncomfortable for staff and employees.
Therefore, it’s important to humidify clean room environments in a regulated and consistent manner to maintain and maximize the operation output at desired levels with ease. Here are other benefits of controlling humidity in your cleanroom!
Clean room environments are designed to be free of dust, unwanted bacteria, and other contaminants to allow the production of sensitive items like electrical components. Unfortunately, these conditions are impossible to achieve without proper humidity control. As a result, cases of workplace illnesses and employee absenteeism are likely to increase. However, if the space has regulated humidification, these cases will reduce since the bacteria will have more limited time airborne.
Clean rooms require high-precision high-control environments to ensure material consistency and product quality. This can be accomplished by ensuring the space has a proper Relative humidity of about 40 – 60% as it provides balanced levels that protect the items against overly most/ dry conditions. At the same time, this helps to prevent unwanted issues like cracking, short-outs, and other types of damage. Moreover, this will ensure that the quality of the clean room product is maintained and increased more consistently while reducing the amount of product and material wastage.
Lastly, electrostatic charges develop when conductive components interact with one another. This can potentially lead to a discharge of electrical energy when these currents build-up, which can cause damage or interference to electronics. Even worse, electrostatic discharge can endanger the lives of employees who interact with these areas. On the bright side, maintaining a balanced relative humidity level in a clean room environment reduces the risk of such situations occurring.
Since humidity is relative, a lower temperature will lead to a lower RH (Relative Humidity). So, if you reduce the temperature in a cleanroom environment, the humidity will also reduce. Similarly, dehumidifying a space with an Air Conditioning (AC system) will reduce the surface temperature below the dew point of the clean room’s airstream. Standard refrigeration equipment produces dew points of around 4 deg C (40 deg F) on a regular basis. As a result, the water vapor in the airflow will condense, thus dehumidifying the space. However, the air must be reheated and directed back into the cleanroom via ductwork to maintain the desired room temperature.
A desiccant system draws air through a moisture-absorbing desiccant medium. That way, the air is dehumidified and routed to the clean room environment. Unlike AC systems, desiccant dehumidifiers produce dew points below -18 deg C (0 deg F), which reduces the air moisture beyond what you can achieve with a standard HVAC-grade refrigeration system.
Most consumer-grade desiccant systems collect condensed water in a receptacle that should be emptied. However, commercial systems exhaust the humid air out of the building through the ductwork, giving them higher dehumidifying power. Also, this allows commercial systems to dehumidify a room to lower RH levels even at lower temperatures.
Desiccant systems and air condition systems to control the humidity of a cleanroom aren’t mutually exclusive. Instead, these systems offer the best results when used in conjunction, especially if temperature control is also essential in a clean room. In addition, using an air conditioning and desiccant system to control humidity in a clean room will help to save energy and help reduce the load as well as wear & tear on the HVAC system.
Final Word
Overall, humidity control for a clean room is critical in some applications like pharmaceutical and semiconductor manufacturing. You can either use a desiccant system, or mechanical refrigeration/ Air conditioning system to control and monitor humidity in your cleanroom. Either way, this will play an important role in ensuring cleanroom integrity and meeting the government & clean room specifications.
To learn more about humidity control for clean room environments, contact InnoDez Design & Engineering. Our HVAC specialists will create the ideal cleanroom system design to meet the needs of your cleanroom project in California!
About Author
InnoDez