Research shows that air quality problems in commercial and residential buildings are usually associated with inadequacies in building design and
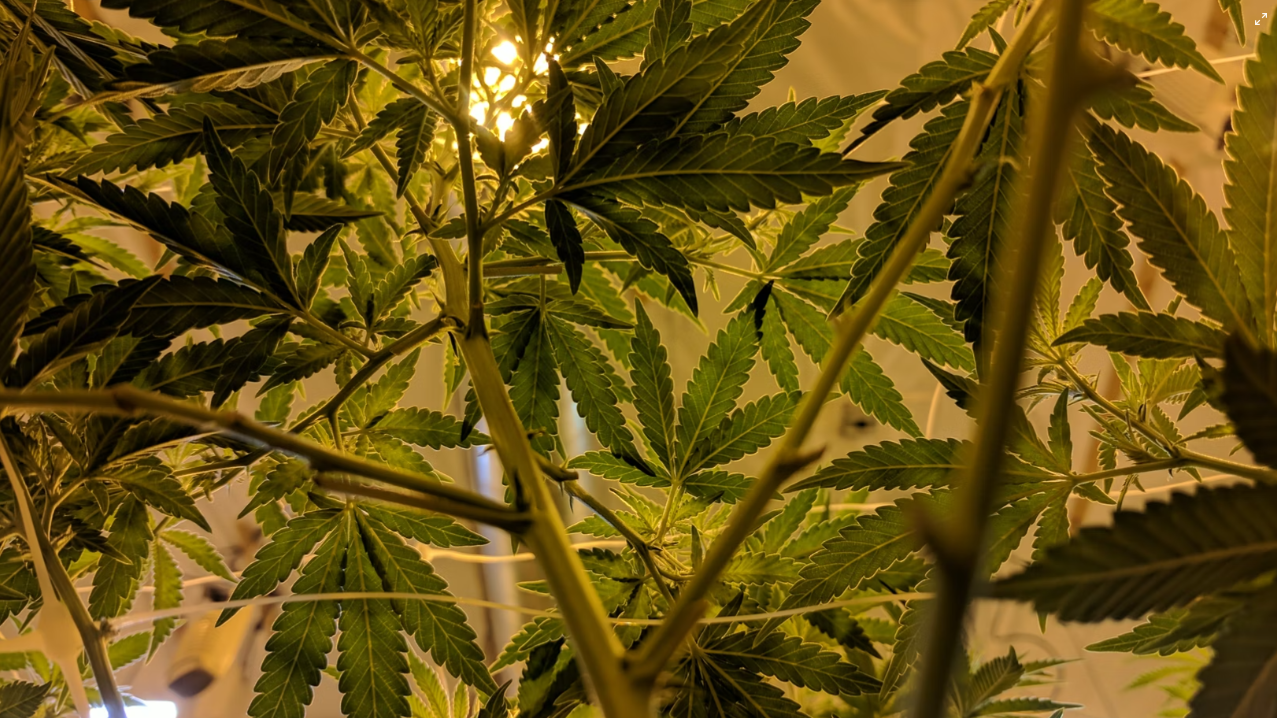
As more states continue to legalize cannabis, commercial cultivation is becoming increasingly popular among many growers. Unfortunately, this evolving industry presents various unique challenges for the growers, especially when it comes to HVAC design for cannabis cultivation facilities.
In essence, quality cannabinoid extraction and cannabis cultivation require high levels of controlled environment agriculture. This involves creating the optimal indoor climate for your growth facility, which can have a huge impact on the success of your business.
Unfortunately, traditional comfort Air Conditioners have proven to be inefficient and ineffective in addressing the environmental challenges of cannabis grow facilities. Underperforming HVAC equipment can cause various environmental-related issues like failed crops, reduced yield, mold, etc.
Therefore, to ensure the success of your growing facility, your HVAC system must address the environmental challenges encountered by these facilities. In this post, we’ll be looking at some of those challenges!
3 challenges to overcome in HVAC & Ventilation design for a cannabis cultivation facility
Marijuana is an adaptable plant that can grow in various habitats. However, it requires specific environmental conditions for each cultivar to express its full potential. For that reason, every factor of climate control is important. Besides, an inadequately designed HVAC system can inhibit growth & development and create an environment that is conducive to pathogens. At the same time, it will significantly affect the beneficial quality of the plant.
Therefore, it’s important to address these challenges as they may jeopardize the success of your business operation. The most important challenges you should address when creating an HVAC design for your grow room include;
The development of Cannabis plants requires a stable temperature of around 70 to 75 deg F. for optimal growth. If the temperature conditions in the grow room get much hotter or colder than this, your plants will be in serious trouble. Drifting outside this temperature range for a prolonged duration weakens the plants’ immune system, makes them more vulnerable to diseases, and inhibits their development.
Unfortunately, maintaining and setting the ideal temperatures in grow rooms is one of the major HVAC design challenges. Besides, the indoor conditions are constantly changing with the maturation cycle of the plant. For that reason, the HVAC system should have capabilities to maintain an interactively evolving environment and adapt to the plant’s growth process.
In addition, oversized HVAC equipment creates temperature fluctuations and swings. This affects the plants directly and changes the relative humidity (RH) in the cannabis cultivation facility. Contrarily, if the system is too small, it will struggle to maintain the temperatures within the optimal range.
Note, supply air temperature shouldn’t exceed 60 deg F. This is because it will place additional constraints on the HVAC system design for indoor cannabis cultivation.
Cannabis plants require high humidity when they’re in a growing phase. In a large grow facility with several different rooms, you’ll always find some crops in the growth stage throughout the year. This poses another challenge in the HVAC design for cultivation facilities since you’ve to control the relative humidity and maintain it within the optimal range.
In most cases, the humidity level of cultivation facilities should be maintained at around 50 – 60%, based on the phase your plants are in. Allowing the humidity to get too high spells disaster. Specifically, high relative humidity in indoor grow facilities creates optimal conditions for mold growth, destroying your crops and profits.
To make it more challenging, the transpiration rate tends to increase as the cannabis plants grow. The excess moisture should be effectively removed from the grow facility. Unfortunately, this poses considerable challenges to traditional climate control systems because the latent load may be as high as 1,000 BTUh for each 10 sq. f of the grow room. Even worse, the late flowering stage needs grow conditions with dew point temperatures ranging from 30 to 40 deg F. This helps to significantly minimize the dehumidification capabilities of vapor compressors.
To sum up, cannabis plants have different humidity needs depending on the growing stage. The exact humidity needs are as follows;
Clone phase: 70 to 80% humidity
Vegetative phase: 50 to 70% humidity
Flowering phase: 50 to 60% humidity
Final weeks of flowering: less than 50% humidity level
Lastly, effective airflow distribution and ventilation design for cannabis cultivation facilities are important for the growth and development of the plant. According to experiments, the relative growth rate is usually optimized at wind speeds less than 3.5 ft/s. Airflow increases stem conductivity and height while reducing the rigidity and strength of the stem.
In addition, the angle at which the wind hits the cannabis plants is important since it affects the transpiration rate. For instance, air moving downwards increases both stomatal and cuticular transpiration rates regardless of the vapor pressure deficit. This is because it creates low pressure on the bottom side of the plant’s leaves.
Conclusion
Creating an HVAC design for commercial cannabis cultivation has several challenges. However, with the right HVAC system for your grow facility, you can easily control or eliminate most of these challenges linked to indoor growing. Moreover, these challenges present opportunities for HVAC professionals to explore the newest technology, show their expertise and fulfill the growers’ needs.
If you’re planning to undertake a commercial cannabis project in California, contact Innodez Design & Engineering. Our HVAC design professionals will use their engineering skills to create an HVAC design that guarantees the vitality of your plants throughout the year while keeping the operating costs down!
About Author
InnoDez