Construction industry affects the environment in all stages; from mining processes used for materials, to the waste produced by the
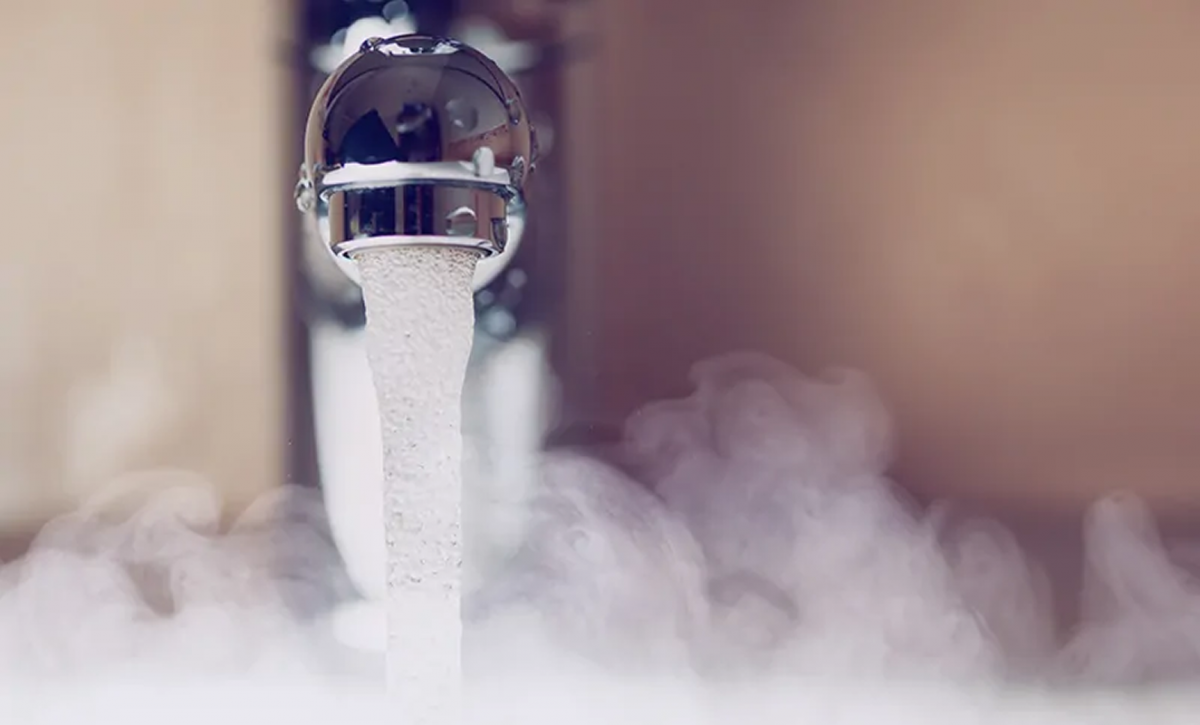
Domestic hot water systems, also known as DHW systems make up a very large part of energy consumption in New York City structures. DHW makes up 12% of the total energy utilized by structures subject to the Benchmarking Law. Within the multifamily residential sector, this number increases to 15%.
Most domestic hot water systems function using either heating oil or natural gas. This makes them one of the main sources of greenhouse gas emissions in NYC. When compared with multifamily residential structures, high-rise buildings have a significantly lower DHW consumption, accounting for just 4% of total energy consumption.
System performance is a concept with a broad definition. Especially dealing with domestic hot water.
1. To deliver hot water on demand at suitable temperatures for the requesting application. For instance, if water gets delivered too cold, taking a shower can be uncomfortable and detrimental to your health. But if the water is too hot, it can even be dangerous. In some cases, DHW systems produce water at the correct temperature but need time to get to that point. Especially when they are off for long idle periods. What causes this problem, that the water in the pipes between the heater and the point of use has had time to cool down in between uses.
2. Using very little energy and minimizing operating costs. By upgrading to a DHW system with higher efficiency, using smart controls, or lowering the water temperature set point, lower operating costs are achieved.
3. Reducing emissions while in operation. This is generally accomplished by decreasing energy usage, and by employing less carbon-intensive heating technologies. For instance, natural gas creates significantly fewer emissions than fuel oil, depending on the heating load. So you can get a Con Edison rebate for this conversion.
Simply put, a top-of-the-line DHW system produces hot water on demand at the correct temperature. It does so while offering lower operating costs and regulating greenhouse gas emissions. However, delivering these calls for more capital, since both environmental stewardship and energy efficiency have a cost.
Energy audits mandated on buildings by Local Law 87 of 2009 have shown a fundamental flaw in the design process of Domestic Hot Water Systems (DHW). This flaw affects how the systems operate in NYC buildings. In a good number of cases, space heating and domestic hot water use the same boiler. That is not a problem when the DHW load and the combined space heating requires full boiler capacity. (but performance can get affected greatly when the system pulls only hot water.)
The problem is, that the boiler often runs at part load inefficiently. In certain cases, boilers operate at full capacity even if the space heating load gets reduced or eliminated. Sadly, 80% of multifamily buildings in New York City still use DHW systems and combined space heating. (though this configuration is more prevalent in older buildings.)
The annual fuel consumption of these buildings increases by 10,000 BTU per square foot on average when compared to similar buildings with two separate systems. The benchmarked space in multifamily buildings amounts to 1.16 billion ft2.
If we assume that 928 million ft2 of are served by both systems, the chance to save fuel is equal to 9,280 billion BTU per year!
The most typical configurations in DHW systems and combined space heating are tankless coils and indirect heat exchangers.
Tankless coils heat water by delivering it directly into a coil in the boiler itself. This currently serves 35% of audited structures. The fuel consumption of tankless coils is around 27% higher than that of separate DHW systems. This is equivalent to 67.5 kBTU/ft2 every year.
Indirect heat exchangers function between the DHW storage tank and the space heating boiler. This serves about 25% of audited structures, consuming 16% more fuel when compared with separate systems. Buildings with these systems consume 62.3 kBTU/ft2 on average.
Dedicated DHW systems show variations in production according to their design. Buildings equipped with DHW systems that utilize a direct-fired hot water tank consume 50.7 kBTU/ft2. Comparatively, buildings that have the tank and boiler set up as separate components consume 57 kBTU/ft2. Notably, in both cases, fuel consumption is significantly lower than in combined systems.
Conclusively, DHW systems based on fossil fuel tend to be more efficient, utilizing a direct-fired hot water tank independently from the space heating system. Natural gas emits the most moderate emissions (117 g CO2 per million BTU, 27% less than emissions emitted by heating oil (161.3 g CO2 per million BTU).
If you are considering using both systems and combined space heating… Consult a professional first before making a decision. If the cost of ownership associated with the new system is greater than the “business as usual” scenario, consider other upgrades for energy efficiency first.
In New York City, electricity is very expensive. As a result of this, the cost of resistance heating quickly becomes restrictive. However, electric DHW systems can considerably contribute to set emissions reduction targets of the city. This is partly because the power can come 100% from renewable sources. Resistance heaters cannot match the operating cost of gas or oil boilers. But high-performance heat pumps, on the other hand, can match their running costs without harmful emissions.
Tankless resistance heaters are cost-effective in smaller applications. That is if they get installed at the point of use. They use inefficient resistance heating, though. Other than that, they are cost-effective, simple to install, and they compensate for their high running costs by only working in short bursts when applicable.
If you own a plumbing fixture in your building where hot water is seldom needed, an electric tankless heater can save you money on gas lines. New York City building audits have shown that point-of-use tankless electric heaters are very common in office buildings. Therefore, they make a convenient option, and domestic hot water systems only represent 4% of energy use in the office sector.
Domestic Hot Water Systems (DHW) incorporates many other components beyond the boiler or heat pump. Reducing the heat loss in your piping and applying water-saving plumbing fixtures can help achieve greater savings. Bear in mind that saving hot water lowers two of your utility bills. (The electric or gas bill, and the water bill, depending on what you use for domestic hot water.)
About Author
InnoDez