Choosing your favorite decorative pendant for a home seems simple, right? Or even choosing the ideal table lamp that blends
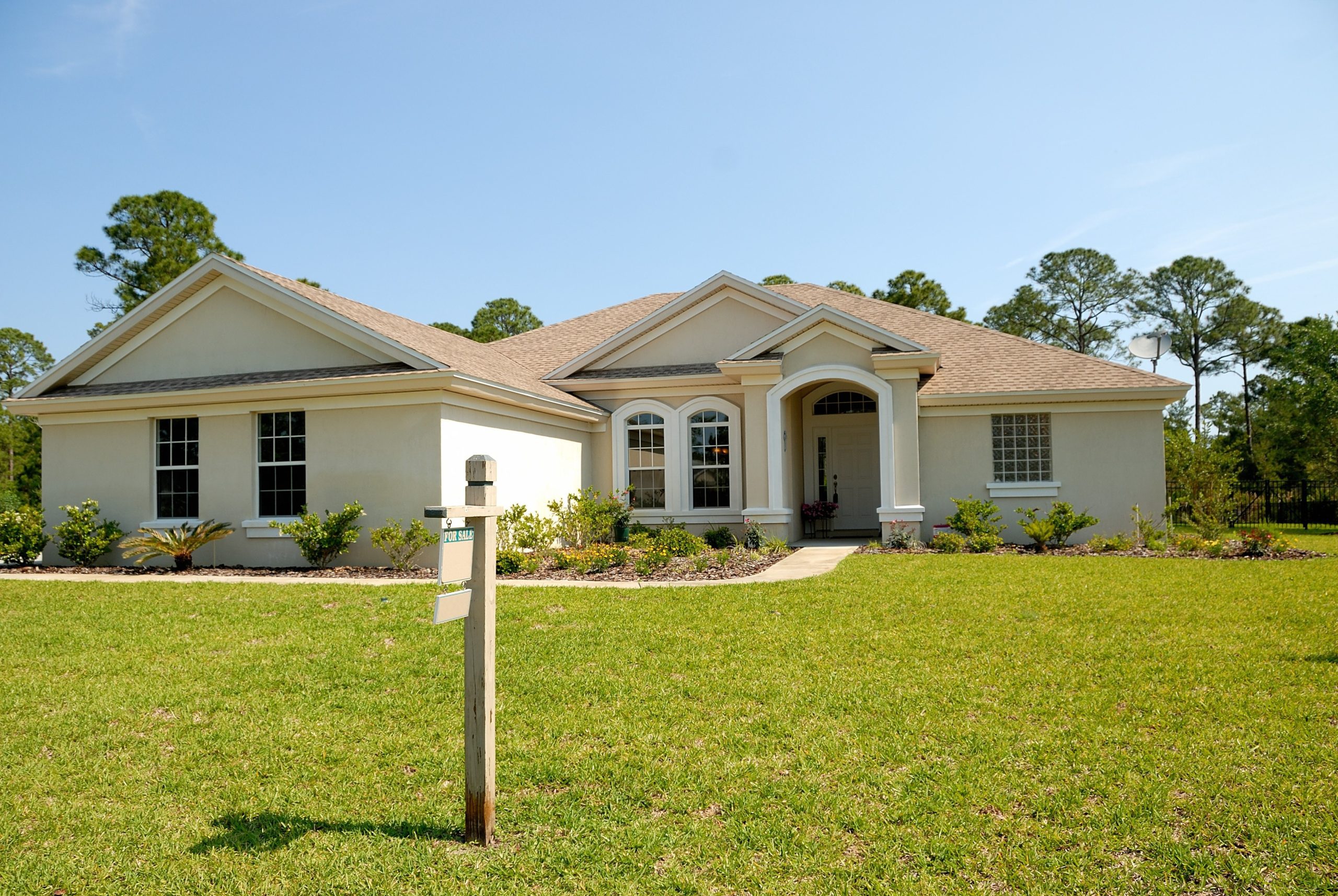
MEP Engineering Design Tips for Multi-family buildings include various residential projects such as senior living, condominiums, apartments, assisted living, student housing, or a combination. Residents of these living spaces have discerning tastes as they want a sense of home, community spaces, and great amenities. For instance, modern multifamily houses include facilities like security systems, fitness facilities, sustainable green initiatives, co-working spaces, etc.
Developers are always looking for ways to improve their market position due to competition in the multifamily industry. However, they also have to consider the cost of labor, materials, and equipment since ROI is important in every construction project. As a result, multifamily building developers are exploring new applications in parking garage configurations, living unit arrangements, and modular design as a way to reduce their costs and optimize their rentable/ saleable square footage. In this post, we’ll show you how strategic MEP (Mechanical, Electrical & Plumbing) design plays a key role in multifamily buildings!
Optimizing saleable/ rentable square footage in a multifamily building is one of the most important factors of the developer’s project-performance model. Generally, Multifamily MEP Engineering Design presents planning challenges in providing the significant space they need while enhancing usable square footage. For that, the design team must come up with creative solutions to optimize the available space, both vertically and horizontally.
Specifically, horizontal distribution systems provide an advantage in reducing the impact of MEP systems on the floor plan’s square footage. For instance, horizontal MEP solutions with distribution in the ceiling like VRF (Variable Refrigerant Flow) systems with ducted fan coils allow HVAC designs to regain square footage. At the same time, such systems take up less space compared to traditional, vertically configured WSHPs (Water Source Heat Pumps) or 4-pipe fan coil configurations. Combining this approach with ductwork terminations at the building’s exterior will save the developer a lot of money.
Alternatively, the HVAC design for multifamily buildings can include vertically configured, stackable MEP systems such as fan coils, VTACs (Vertical Terminal Air Conditioners), and WSHPs. These units are placed on the exterior or adjacent walls of living units whose floor plans mirror one another. This configuration provides various benefits when it comes to ventilation, exhaust, and distribution by using opposing soffits within the unit. Plus, these HVAC units can reduce the additional floor space needed for the distribution of refrigerant/ water systems and share risers.
This approach will offer 2 important benefits. One, the effect will be less prominent visually on the building’s exterior. Secondly, consolidation will reduce the distribution’s complexity within the space.
On a vertical plane, designers are starting to compress the building envelope by reducing the floor-to-floor heights. This involves reducing the amount of ductwork and equipment in the ceiling. In a high-rise multi-family building, minimizing the floor-to-floor height by 6 - 12” will give the building adequate verticality to add an extra floor. As a result, this will substantially increase the saleable/ rentable square footage without increasing the building height.
However, reducing the floor-to-floor height can be challenging when HVAC systems are installed in the ceiling, particularly in wood-framed structures with tight ceiling spaces.
Moving on, you can capitalize on space by running exhaust and ventilation ductwork within the space between parallel joists to the building’s exterior. This will allow the designer to maintain higher ceilings while eliminating shafts that take up rentable square footage.
Overall, these approaches will help you to optimize the saleable/ rentable square footage of a multifamily building. However, the designers must consider how the design might affect the occupants’ comfort inside the units and the trade-offs involved.
Decisively planning the MEP engineering Design within the parking structure in a large development will help you to reduce construction costs and optimize square footage. In a multifamily parking garage, you can accomplish this by reducing excavation depth and floor heights, which puts pressure on piping, electrical, and ductwork configurations. Also, using a design-assist approach will help you achieve this goal since labor and material costs tend to vary widely among contractors. Even better, engaging your general contractor and subcontractors during the design phase will help developers to refine the selection of the materials and accurately estimate the MEP budget.
In addition, the HVAC design can reduce congestion within the parking garage ceiling space and construction costs by modeling the garage fresh-air supply and exhaust using computational fluid dynamics (CFD). The model will reveal how transfer fans perform conventional ducted systems while providing a more predictable performance outcome.
Another emerging trend to enhance space efficiency is to use parking stackers. To be precise, incorporating a packing stacker system helps the developer minimize the depth of excavation and lowers the HVAC costs associated with the project.
Modular design is another way to reduce costs and speed up construction which is becoming increasingly popular in the multifamily building industry. In most cases, it’s less costly to install and procure MEP systems for living units in a manufacturing setting compared to assembling the components on-site.
On the downside, modular construction designs can show visible clues that the structure is prefabricated like double walls and dividing lines. However, working closely with a modular design contractor will help you to select the right craft installation plans and systems to reduce such defects.
In addition, developers must understand the extra complexity layers in the process of pulling permits for modular construction designs. This is because project coordination is another popular challenge that comes with a modular design. Besides, the working relationships in traditional construction design are between the contractor and architect. Therefore, bringing in a 3rd party modular design expert will add an extra layer to your design team coordination efforts.
That aside, the best way to get most of the MEP systems installed as part of the scope of work of the modular design manufacturer is compartmentalization. For instance, with electrical design for multifamily buildings, each unit might have 2 or 3 modular sections that make up a single residential unit. This can be sophisticated since there is one, shared electrical panel with wiring and conduit routed to the other sections in the modular design. In that case, the best option is to have junction boxes that end at the edge of modular connections and route as much conduit as possible into the possible instead of assembling all the wiring within one unit and routing the remaining connections on-site. This will make on-site installation much easier and faster.
As for the HVAC design, self-contained systems are highly efficient for modular construction projects. Nonetheless, split heat pumps with condensers will also work well for such types of projects. If the roof space is a challenge, you can replace the remote condensers on the rooftop with VTAC units to free up space. Alternatively, you can run individual exhaust systems horizontally, thus reducing the vertical shaft systems that add a coordination layer and take up space because of their complexity.
Modular design is also associated with shorter ROI periods and significant cost savings. Therefore, it presents an opportunity for higher-level solutions in the project like individual heat recovery ventilators that save on energy costs and enhance indoor air quality.
Conclusion
New construction methods can be challenging to plan and implement. However, they have substantial rewards, especially in MEP for multifamily buildings, and can be used in future projects.
At Innodez Design & Engineering, we work closely with other design professionals, contractors, owners, and developers to ensure that MEP systems for multi-family buildings are properly coordinated & uninstalled. More importantly, our experienced team of MEP Engineering Design identifies potential conflicts early to ensure the satisfaction and comfort of future occupants.
About Author
InnoDez