Concrete stamping has increased dramatically in demand over the past 50 years. Used in a wide variety of residential and
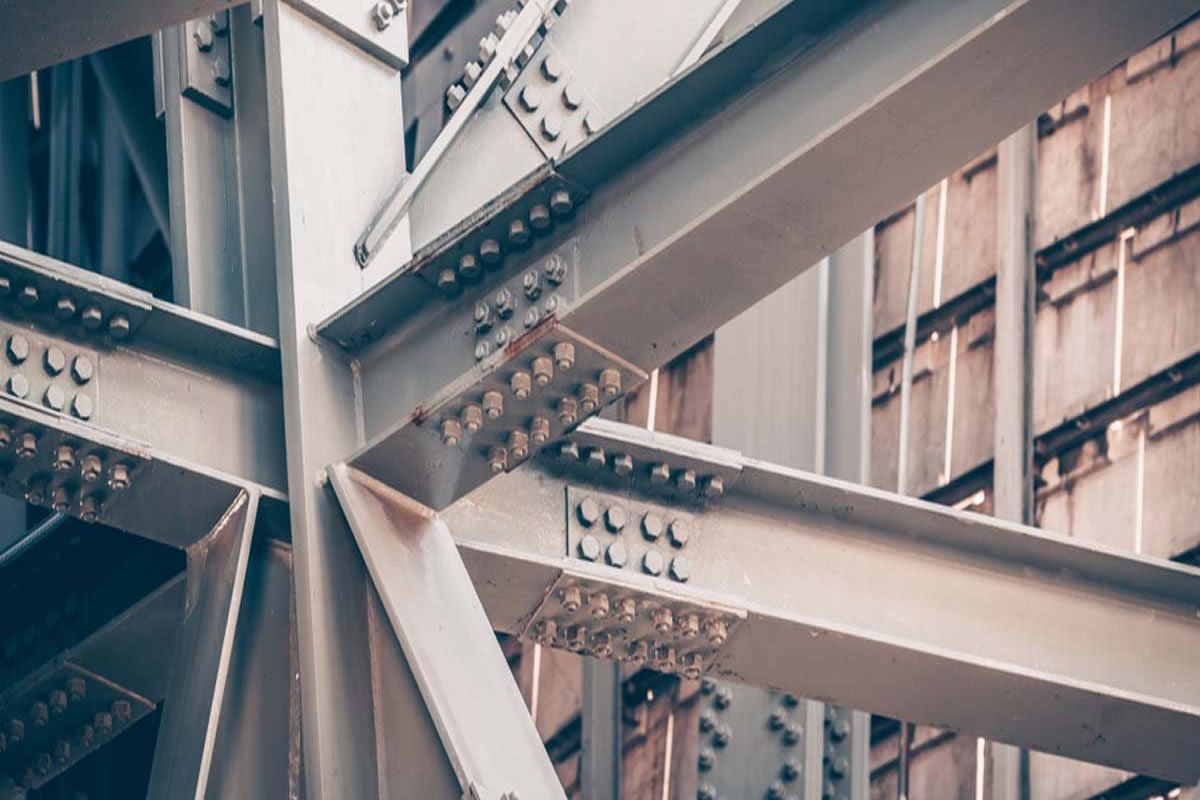
Before engineers start the planning and designing stage of any project, they have to decide what tools and materials are best to work their project with.
While the types of joints that are used in a structure usually are chosen to fit with the overall design.
They have to think about factors like; cost, overall performance, and installation time as well to make the best of their project and whatever budget that they are working with.
Keep reading and we will compare welded joints and bolted joints. 2 main types of joints generally used to connect elements made of thermoplastics and metals. Joint design is one of the key elements involved with steel construction.
In the construction industry, various welding methods are used. Welded joints are made by fusing two elements together with extreme heat and letting them cool down again. According to the American Welding Society (AWS), there are five types of welded joints that can be welded:
Butt
Corner
Edge
Lap
Tee
All of these types of joints depend on how the welded elements fit together.
Bolted joints utilize fasteners that will keep structural elements in one position. They are secured with screw threads instead of a weld.
There are two types of tension joints and shear joints. As in many other engineering decisions, both weld options have their own set of pros and cons.
The price for both bolted and welded joints will vary by project. But for the most part, bolted joints are a less expensive option. The cost of bolted joints has to rely on steel prices. But the manufacturing process flows more efficiently and allows you to automates the manufacturing process of welded joints.
The installation of welded joints must be done by certified welders, who, of course, work on hourly rates.
Since the labor cost for workers to tighten bolts is much lower than skilled welders, bolted joints will normally be the best option if you’re on a tight budget.
Welded joints, in general, are stronger than bolted joints, which, if you know anything about welding, you might have guessed already. This is mainly because the material doesn’t have holes in them as bolted joints do. So if the strength of your project is a major concern, you would want to go with welded joints. When the performance of your structure matters, this is one case where you would want to just choose quality over cost.
With bolted joints, inspectors have to make sure that the bolt is at least flush with the fastener holes or sticking out some. The bolts cannot be screwed in lower than the edge of the hole that they are secured in.
Inspectors also ensure that bolts have are tight enough, and check for any that have snapped off.
Depending on the project, welding inspection methods can vary. A visual inspection is commonly the method used, there are inspections done before, during and after the welding process. There are other methods that require specialized equipment, that are more expensive than visual inspections, and require inspectors that are AWS certified to perform them, therefore the inspection process of welded joints is generally more expensive and tedious.
Due to the continuity of the cross-section, welded joints make more rigid fasteners than bolted joints. However, bolted joints are generally fastened using plates or angles, allowing the slight deflection that the structural elements need to transfer heavy loads, adding flexibility to the equation allowing more movement and reduce structural stress.
But then there is a drawback with bolted joints. And that is that the additional hardware required to install them. This limits the type of applications that they can be used on.
Welding tends to be more versatile, since just about any two surfaces can fit together in a weld. Other elements can be easily fastened onto existing unions.
Construction managers have to be aware of important differences between installation procedures of both types of joints in order to carry out the project effectively.
Bolted joints are usually installed with an impact wrench or a spud wrench and are easier to work with and easier to repair. This helps save time in cases where unexpected situations arise.
Welded joints, because they are done manually by a certified welder require various equipment types and energy sources depending on which type of weld is called for. A shielded metal arc welding (SMAW) the type of equipment that is most used. In SMAW welding, an electric arc is made between coated metal electrodes and whatever steel components are being welded.
The welding can generally be performed in a factory or at the job site, both of which have strict safety and quality requirements to adhere to.
Like with any welding application, precautions are necessary to avoid burns, inhalation of fumes, UV radiation exposure, vision damage, and electric shock. Bolting, on the other hand, has only one danger, and that is working at various heights.
To summarize, there is somewhat of a loss of structural performance with bolted joints, but bolted joints have an advantage of cost and simplicity over welded joints. Comparatively, welded joints are stronger but the cost is higher and at times, difficult to handle.
When it comes to choosing a superior option, the answer is that which joint you end up choosing will be reliant on your project requirements and your builder’s preferences.
About Author
InnoDez