The term mixed-use building refers to the structure which combines itself for various purposes under a single roof. To make
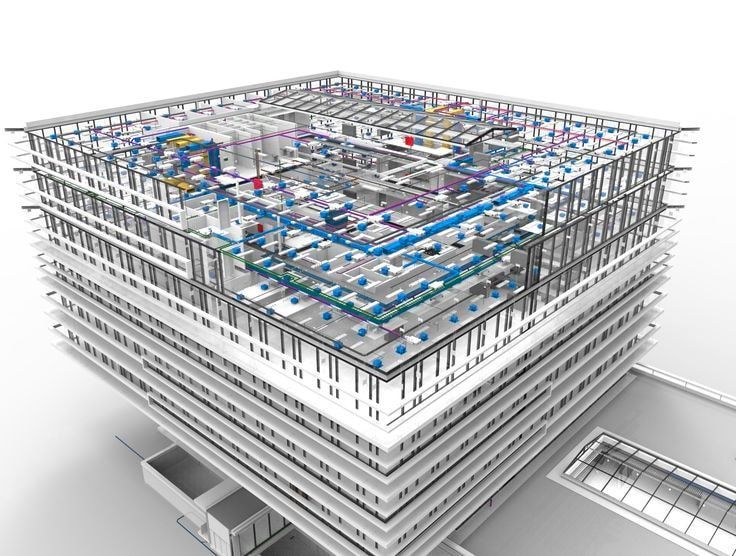
In the rapidly evolving construction industry, prefabrication has emerged as a game-changer for faster project delivery. This article explores the rise of prefabricated Mechanical, Electrical, and Plumbing (MEP) systems and discusses the advantages and considerations of implementing this innovative approach.
Prefabrication involves assembling MEP components off-site and delivering them to the construction site, ready for installation. By streamlining the construction process, prefabricated MEP systems offer several significant advantages. Firstly, they reduce on-site construction time, minimizing disruptions and allowing for faster project completion. Additionally, the controlled environment of off-site fabrication ensures higher precision, quality, and consistency in the assembly of MEP systems.
However, as with any construction method, there are also considerations to keep in mind. Factors such as transportation logistics, coordination with other trades, and potential limitations in design flexibility need to be carefully evaluated. By leveraging the benefits of prefabricated MEP systems, project stakeholders can achieve quicker project turnaround, enhanced quality control, and increased efficiency. Join us as we dive deeper into the advantages and considerations of this increasingly popular construction methodology.
One of the primary advantages of using prefabricated MEP systems is the significant reduction in on-site construction time. By assembling the components off-site, the time spent on-site for installation is greatly reduced, allowing for faster project completion. This is particularly beneficial in projects with tight timelines or in areas with limited access or space constraints, where traditional on-site construction methods would be more time-consuming and disruptive.
Another key advantage of prefabricated MEP systems is the enhanced quality control achieved through off-site fabrication. In a controlled manufacturing environment, the assembly of MEP components can be meticulously monitored and inspected, ensuring a higher level of precision and consistency. This translates to fewer on-site errors, reduced rework, and ultimately, a higher-quality final product. By minimizing the need for on-site modifications, prefabrication also helps to reduce material waste and improve sustainability in construction projects.
Prefabrication also offers significant cost savings, both in the short and long term. By streamlining the construction process and reducing on-site labor requirements, prefabricated MEP systems can lead to lower overall project costs. Additionally, the improved quality and reduced maintenance needs associated with prefabricated systems can result in long-term cost savings for building owners and operators. This makes prefabrication an attractive option for project stakeholders seeking to optimize their budgets and achieve better value for their investments.
While the advantages of prefabricated MEP systems are compelling, there are also several considerations that must be taken into account when implementing this approach. One of the primary challenges is the coordination and integration of prefabricated components with the overall construction process and other trades.
Effective communication and collaboration between project stakeholders, including architects, engineers, contractors, and suppliers, are crucial to ensuring a seamless integration of prefabricated MEP systems. This requires careful planning, scheduling, and coordination to ensure that the prefabricated components are delivered to the construction site at the right time and in the correct sequence, without disrupting the work of other trades.
Another consideration is the potential limitations in design flexibility when using prefabricated MEP systems. While these systems offer the advantage of standardization and off-site assembly, they may not always align perfectly with the unique design requirements of a particular project. Project teams must carefully evaluate the available prefabricated options and work closely with suppliers to ensure that the selected systems can be integrated into the overall design without compromising functionality or aesthetics.
One of the primary ways that prefabricated MEP systems accelerate project delivery is by reducing the time required for on-site construction. By assembling the components off-site, the project team can significantly streamline the installation process, eliminating the need for extensive on-site coordination, sequencing, and assembly.
This off-site fabrication approach also allows for concurrent work, where various components of the MEP system can be manufactured simultaneously, rather than being dependent on the progress of on-site construction. This parallel processing can shave weeks or even months off the overall project timeline, enabling project teams to deliver the completed facility to the client much faster than with traditional construction methods.
Additionally, prefabrication can help mitigate the impact of weather-related delays and other site-specific challenges that can often arise during on-site construction. By moving a significant portion of the work off-site, project teams can better control the manufacturing environment and minimize the disruptions caused by external factors, further contributing to the acceleration of project delivery.
In addition to the time-saving benefits, prefabricated MEP systems can also result in significant cost savings for construction projects. One of the primary ways this is achieved is through the reduced on-site labor requirements. By assembling the components off-site, the need for specialized on-site tradespeople is greatly diminished, leading to lower labor costs and reduced overhead expenses.
Furthermore, the enhanced quality control and precision inherent in prefabricated systems can translate into long-term cost savings for building owners and operators. With fewer on-site errors and a higher level of reliability, the maintenance and repair requirements for prefabricated MEP systems are often lower than their traditional counterparts. This can result in substantial savings in operating and maintenance costs over the life of the building.
Prefabrication can also help mitigate the impact of material waste and supply chain disruptions, which can be significant cost drivers in traditional construction projects. By optimizing the manufacturing process and leveraging the economies of scale, prefabricated MEP systems can often be produced more cost-effectively than custom on-site assemblies. This, combined with the reduced material waste, can lead to overall project cost savings that make prefabrication an increasingly attractive option for project stakeholders.
While the advantages of prefabricated MEP systems are compelling, there are also some challenges and limitations that must be considered when implementing this approach. One of the primary challenges is the coordination and integration of the prefabricated components with the overall construction process and other trades.
Effective communication and collaboration between project stakeholders, including architects, engineers, contractors, and suppliers, are crucial to ensuring a seamless integration of prefabricated MEP systems. This requires careful planning, scheduling, and coordination to ensure that the prefabricated components are delivered to the construction site at the right time and in the correct sequence, without disrupting the work of other trades.
Another consideration is the potential limitations in design flexibility when using prefabricated MEP systems. While these systems offer the advantage of standardization and off-site assembly, they may not always align perfectly with the unique design requirements of a particular project. Project teams must carefully evaluate the available prefabricated options and work closely with suppliers to ensure that the selected systems can be integrated into the overall design without compromising functionality or aesthetics.
To successfully integrate prefabricated MEP systems into construction projects, project teams should adhere to the following best practices:
By following these best practices, project teams can effectively leverage the advantages of prefabricated MEP systems while mitigating the potential challenges and limitations.
As the construction industry continues to evolve, the use of prefabricated MEP systems is expected to become increasingly prevalent. Advancements in technology, such as Building Information Modeling (BIM) and automated manufacturing processes, are driving the development of more sophisticated and customizable prefabricated solutions.
One emerging trend is the integration of smart technologies into prefabricated MEP systems. This includes the incorporation of sensors, data analytics, and remote monitoring capabilities, which can enhance the performance and efficiency of building systems. By leveraging these smart technologies, building owners and operators can optimize energy consumption, improve maintenance schedules, and enhance the overall user experience.
Another trend is the increased focus on sustainability and environmental impact in the design and manufacturing of prefabricated MEP system. Manufacturers are exploring the use of eco-friendly materials, renewable energy sources, and more efficient manufacturing processes to reduce the carbon footprint of these systems. This aligns with the growing demand for sustainable construction practices and the drive towards net-zero emissions in the built environment.
In conclusion, the rise of prefabricated MEP systems has transformed the construction industry, offering significant advantages in terms of faster project delivery, enhanced quality control, and cost savings. By leveraging the benefits of off-site fabrication, project stakeholders can streamline the construction process, minimize disruptions, and deliver high-quality buildings and infrastructure more efficiently.
While there are considerations and challenges to be addressed, such as coordination with other trades and potential limitations in design flexibility, the overall benefits of prefabricated MEP systems make them an increasingly attractive option for construction projects. As the industry continues to evolve, the adoption of prefabrication is poised to accelerate, driven by advancements in technology, a focus on sustainability, and the ongoing demand for faster, more efficient project delivery.
By embracing the advantages of prefabricated MEP systems, project teams can unlock new levels of efficiency, quality, and cost-effectiveness, positioning themselves for success in the rapidly changing construction landscape. As we look to the future, the continued innovation and refinement of prefabricated solutions will undoubtedly play a pivotal role in shaping the way we build and deliver projects in the years to come.
About Author
Xhuljo Jakup